- Aman Kumar
- July 21, 2022
Deep Learning-based Defect Detection in Telecom Towers
Introduction
Telecom towers are considered critical infrastructure for ensuring nation-wide communications. Telecom Service Providers rely on these towers for hosting their antennas, power modules and other communication components. To ensure uninterrupted communication services, regular maintenance and upkeep of these towers is required.
To gather information about tower health, a person is required to be sent up the tower to manually check for numerous types of defects. Common defects related to telecom towers include missing nuts, bolts, plates, joints, broken or warped beams, corroded parts, antenna damage or misalignment etc. This method of manual inspection is both time consuming and potentially hazardous due to the need for humans to operate several hundreds of feet above the ground.
An alternative to physical human access is the utilization of drones, carrying camera payloads for the inspection of these towers. The drone can capture the video feed of the various faces of the tower which can then be inspected using automated detection techniques. Ignitarium’s TYQ-i™ platform employs Deep Learning techniques to perform advanced analytics of civil infrastructural assets like telecom towers.
This article describes the use of TYQ-i software to perform the critical task of detection of missing bolts and perhaps equally importantly, their unique identification and tagging across multiple frames of a video to allow a maintenance crew to quickly pinpoint a specific defect without duplication.
Pipeline
The processing pipeline consists of several stages starting from the ingestion of the drone footage till the generation of results. This section describes the key modules involved in allowing accurate detection of defects
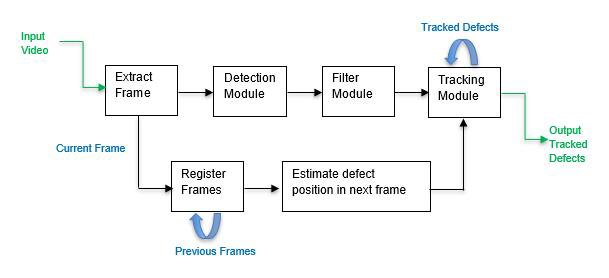
Fig. 1: Processing Pipeline
1. Detection
We utilize a CNN-based image segmentation network due to its ability to both detect as well as localize small scale defects. The model used for the semantic segmentation of defects is Mobilenet-unet. The model utilizes a Mobilenet backbone and then uses conv-blocks and up-sampling layers to build upon the segmentation map.
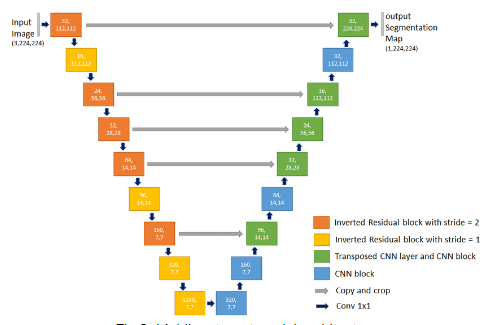
Fig 2: Mobilenet-unet model architecture (source)
The CNN requires labelled data to be able to detect anomalies from the drone videos. Labeling is done hierarchically, building up components that constitute a tower – like the tower face, beams, plates, bolts, and holes, as shown in Figure 3.
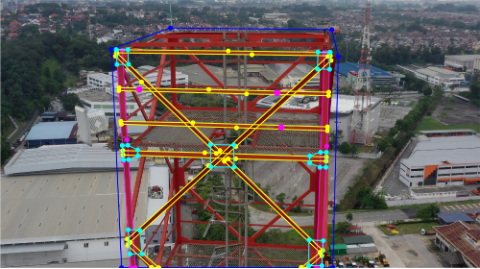
Fig. 3: Labeling tower, beams, joint and holes in the frames
We use categorical cross-entropy loss and Adam optimizer for our model and train for 50 to 100 epochs with augmentations. We utilize brightness, contrast, rotation, flipping and other augmentation techniques during training to improve model generalization.
2. Filter Module:
The detection module identifies the defects in the image. But some defects are false positives. We can utilize some properties of the defects to help us in improving the Intersection of Union (IoU) score and decrease the false positive rate. We utilize the following two filters:
- Length-Breadth Filter: The defects obtained after the detection module are further checked against length and breadth thresholds. If the defects are below the required thresholds, they are removed. This helps in improving some small stray detections that occur due to noise.
- Check-inside-Parent Filter: We also know beforehand that the defects will occur only inside the boundary of the tower structure. To eliminate any false detections in the background, we use this filter to first do detection of the tower (the parent node) and then use the resultant tower region to filter out extraneous defects.
3. Tracking and Registration:
After the filter component, the next part in the pipeline is the tracking module. The tracker can save the location of a detected defect and then searches in the neighborhood, in the next frame of the video. Using image registration techniques, the expected location of the defect can be estimated in the next frame. This is done by making the moving image overlap on top of the stationary image. Then we search within the neighborhood of the estimation. If the center of the new defect falls within this neighborhood (within a pre-defined margin of error), we designate it as an existing defect, instead of a new defect. Using this method, the tracker module can dynamically maintain the location of every defect in its history map.
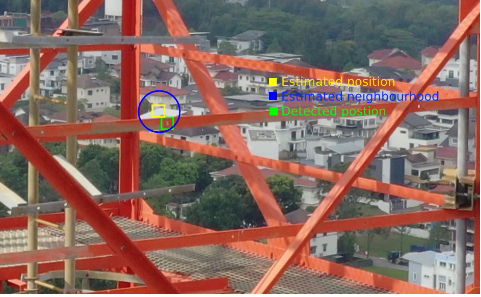
Fig. 4: Estimation of defect using registration
Fig. 4 shows a tower hole highlighted by the green bounding box. By using the last frame’s shift, the estimated bounding box is obtained and marked as yellow. Some edge cases require special handling during tracking. We keep a history of 5 for every defect; if the defect eludes detection in the current frame but is still detected in the next 4 frames, we will be able to track it as the same defect. This bookkeeping allows us some flexibility in case of false-negative detection and provides a layer of robustness to the tracking module.
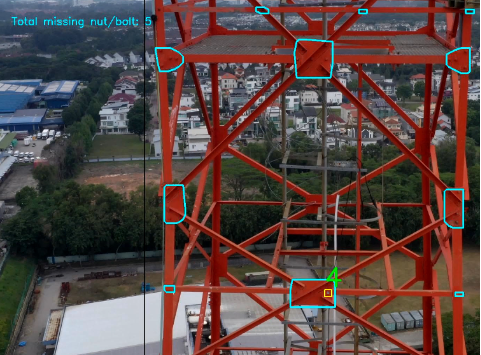
Fig. 5: Cumulative results from Tower Face 1
Fig. 5 shows visual results after the entire video of one face of the tower has passed through the complete software pipeline. The total number of missing bolts (in this case 5) are uniquely identified and stored in a database.
View the demo video here.
Conclusion
Using the TYQ-i platform, routine inspection of telecom towers can be automated, and specific components of interest can be automatically monitored for anomalies. This saves resources and time and can be used by telecom companies to ensure better upkeep of their infrastructure and better service delivery to end consumers.
References:
- Tulbure, Andrei-Alexandru et al. “A review on modern defect detection models using DCNNs – Deep convolutional neural networks.” Journal of Advanced Research 35 (2021): 33 – 48.
- Sandler, Mark, et al. “Inverted residuals and linear bottlenecks: Mobile networks for classification, detection and segmentation. CoRR abs/1801.04381 (2018).” arXiv preprint arXiv:1801.04381 (1801).
- A Guide to Tower Inspection Using Drones (2021). https://pilotinstitute.com/drone-tower-inspections/