- Arjun Kumar and Sam Verghese
- November 10, 2021
Enabling safety in workplaces with mobile robots using Virtual Fencing
Robots have mastered every position imaginable in the post-pandemic world, from forklifts, trolley haulers, and industrial floor scrubbers in factories to delivery bots on the curb (you can read all about it in our blog- link here).
Human-robot interactions have increased dramatically in factory environments, posing a safety risk. It’s challenging to figure out which technology, solutions, and workplace activities to invest in to get the best return on investment in terms of profit, productivity, and safety. Technology by itself does not always lead to improvements and depending simply on safety measures and education is not the solution.
There is a pressing need for safe autonomous navigation to be integrated as a vital component of the robotics software stack, ensuring that it is not only robust and efficient but also functionally safe.
Functional Safety Standards
The underlying notion behind functional safety is that the whole system should be dependable even if something unexpected happens. IEC 61850 has evolved into many safety standards for various applications (Read about Functional Safety for Automotive – link here).
An operator or manufacturer of automated guided vehicles or automated guided vehicle systems (multiple automated guided vehicles) must comply with the specifications of ISO 3691-4:2020. This standard establishes how to assess the automated operations of the vehicles and provides the standards for safety functions. The required performance level for vehicle monitoring functions, different operating modes, and the brake controller are also specified. Both The American National Standards Institute (ANSI) and the Robotic Industries Association (RIA) recently released a new safety standard – for Industrial Mobile Robots – Safety Requirements ANSI/RIA R15.08-1-2020 (R15.08) that outlines safety requirements for various types of mobile robotic systems, including AMRs. R15.08 further clarifies the concept of an ‘AMR’ and distinguishes between other sorts of mobile robots, which is essential for R15.08 to work properly.
Implementors of Safety Standards
AMRs promote a safe workplace by defining collision-avoidance procedures, establishing safety zones, and obstacle detection, as well as restart intelligence. However, these are contingent on the robot maker, integrator, and owner having a thorough understanding of what constitutes a safe working environment.
It’s vital to keep in mind that purchasing a safe robot from a robot manufacturer is merely the first step in increasing workplace safety and lowering risk. When integrating robots into processes, the robot owner and integrator must collaborate to verify that AMRs can be utilized safely.
The robot’s owner is responsible for purchasing a robot that is deemed safe and follows current safety norms and standards. This necessitates the robot owner’s knowledge of workplace safety risks and dangers, as well as how AMRs may be integrated into the workplace and the best approach to train personnel on how to interact with and operate AMRs.
The robot integrator is in charge of evaluating the entire workspace or system to ensure that AMRs are safe to use. This includes knowing how elements like entrances, other equipment, high-traffic zones, transfer points, and other system aspects affect AMRs’ capacity to function properly.
Environment
As previously stated, the operating environment, like AMR’s built-in safety measures, plays a critical part in keeping humans safe from unintended harm. Hence, understanding what constitutes safe operation and how AMRs fit into it is crucial.
For the AMR to operate in a factory workplace, the environment can be separated into distinct zones as below:
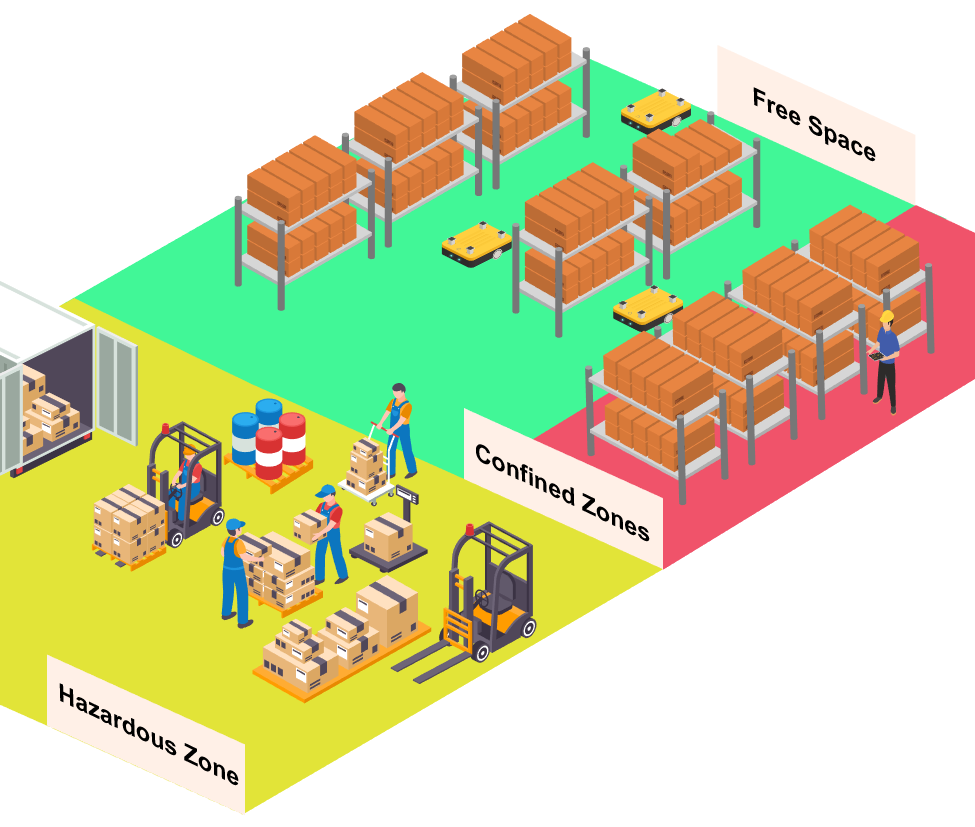
- Free space of a factory workplace refers to the area where the mobile platform can plan a path
- Operating Hazard zones – spaces with insufficient clearance. These are regions where the clearance between the sides of the AMR (or front/back of the AMR) and a barrier, such as a wall, is insufficient to allow a person to escape and could lead to a crushing hazard between the AMR and the hindrance (less than 500 mm). It might also be a location where AMR’s detecting equipment is ineffective. These zones must be properly marked with appropriate signage or, preferably, floor markings. The AMR’s speed in this operating danger zone must comply with ISO 3691-4, and it must transmit extra audible or visual warnings.
- Load Transfer Zones – These are the stations where loads are transferred. When load transfer stations are located outside of restricted or constrained zones, they must be constructed to protect people from being injured by the AMR’s rigid components or its cargo.
- Confined Zones— At any speed, these are zones with insufficient clearance and where the AMR detecting devices may be bypassed. The limited zones must be identified and surrounded by fixed guards and are at least 2.1 meters tall.
- Keepout zone or Restricted zones or No-go Zones–
Zones that are not part of the public domain (public domain is where the mobile platform can plan a path). These are zones with insufficient clearance that are not covered by the AMR detection devices’ monitored space (monitored space is the volume around the AMR that perception systems can monitor). Only authorized individuals are permitted to enter.
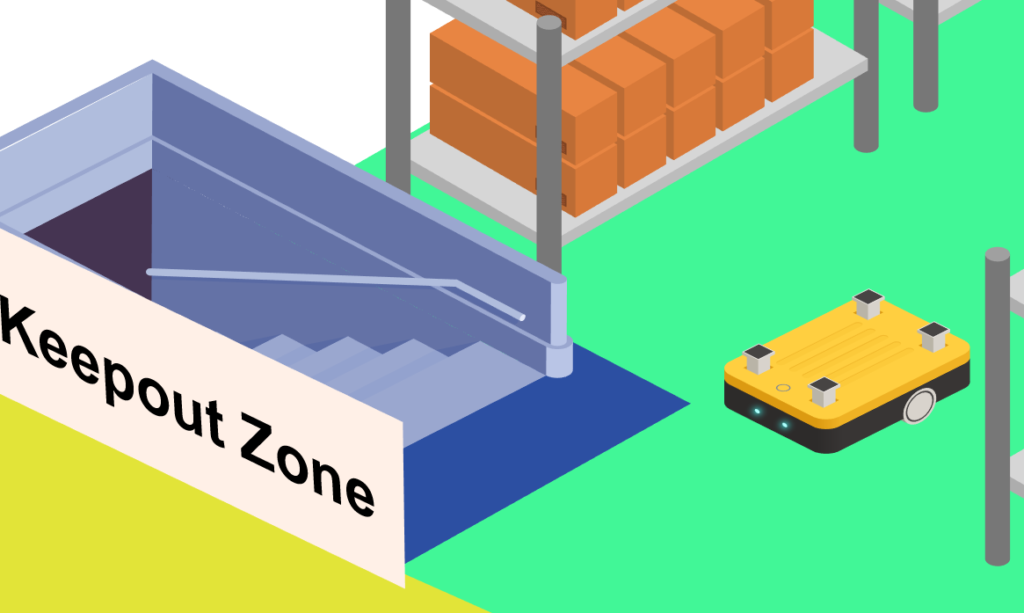
Keep out zones that are inside the AMR’s working area are commonly associated with fall hazards. These are some of the dangers:
- The edge of a loading dock or ramp.
- Entrance to downward stairs.
- Any other vertical drop that exceeds the AMR’s maximum step height.
There are areas where it is unsafe for the AMR to operate which are termed as Environmental Hazards.
Physical obstacles like barriers that the AMR can identify correctly with its scanning laser to prevent it from driving near the hazard, are used to limit this risk. A barrier must be sturdy enough to withstand a fully loaded AMR traveling at its maximum speed, in addition to being immediately identifiable.
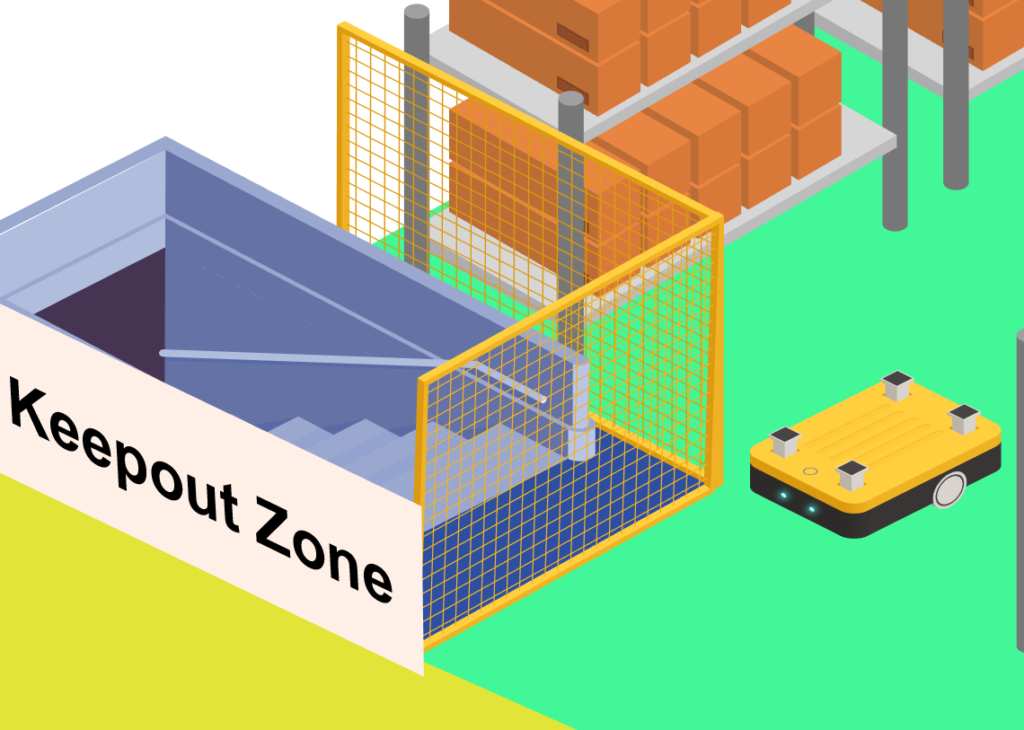
Virtual Fence
One of the most useful safety features used is logical barriers or virtual fencing – a technique used to set up an invisible barrier in the real world to prevent AMRs from closely approaching a fall hazard and avoids planning a path around the virtual fence. They are generally represented as an image file but they will only work if the AMR has access to your environment map, which you can generate with an image editor and share with the robot. This allows robots to be restricted from wandering off in certain sections of your warehouse and remain in others, which is especially useful when you want them to continue working in a primarily mapped area.
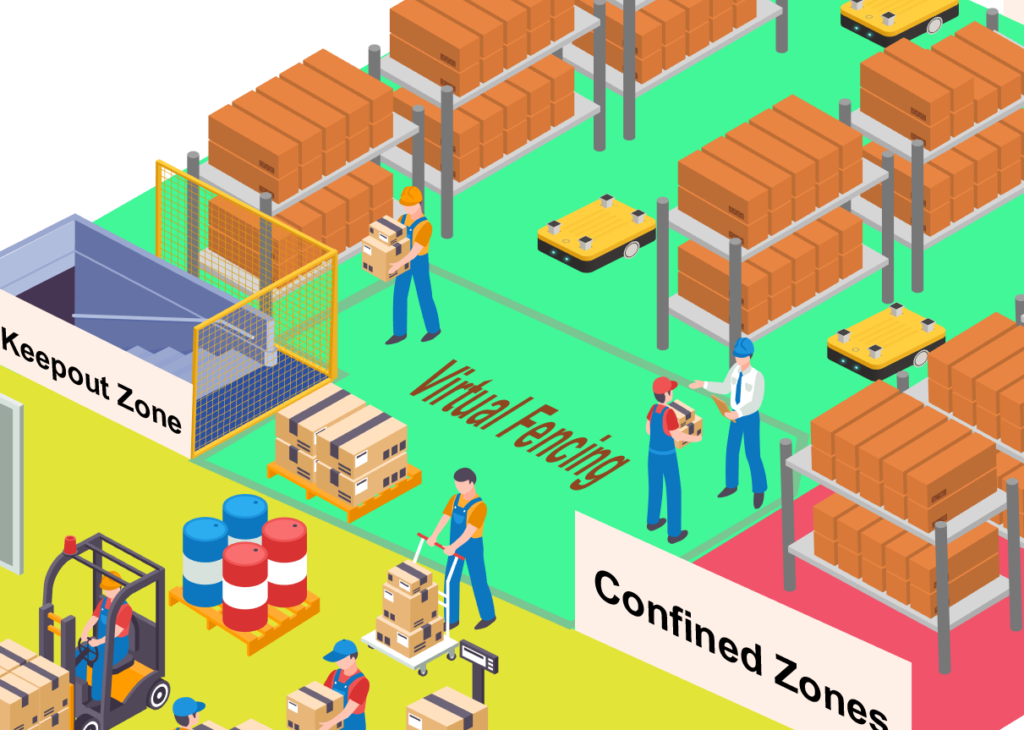
Typically to enable autonomy, AMRs require a map of the operating environment to navigate safely. These maps are built using Simultaneous Localization and Mapping (SLAM) algorithms such as Gmapping, one of the popular open-source algorithms developed by OpenSLAM. The gmapping package is a ROS wrapper of Gmapping which generates a 2-D occupancy grid map using 2D laser scan or Depth Camera and Robot Wheel Odometry. The generated maps are stored as grayscale images in Portable Gray Map (PGM) format by default.
The popular mobile robotics company, OMRON Robotics uses Mobile Planner software which is the control center for creating maps, managing robot configurations and so on. Using their UI based tools, a user can add forbidden zone or virtual zone to the map.
Here, let’s look at how we can use ROS costmap2D plugins to create a virtual obstacle layer in the global costmap and Rviz plugins to map the mouse/touch event which can then be used for marking the obstacle information on the map.
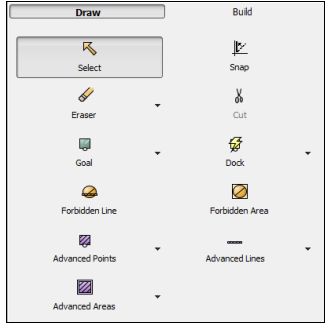
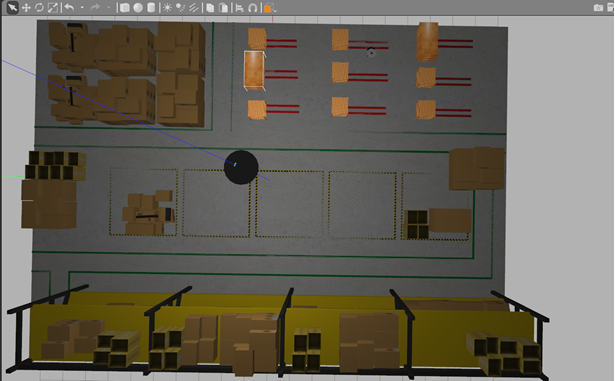
As AMRs are dependent on the map of the warehouse environment, any restriction in the area i.e. the area it shouldn’t navigate has to be shared with the AMR beforehand. One such common approach is to add restriction zones to the map by modifying with any image editor as the maps are represented as image files. For example, ROS2 Navigation2 stack uses keepout zones using the Keepout Filter costmap filter plugin.
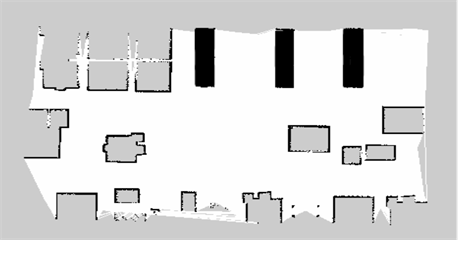
In the keep out zones, we can restrict the robot from planning paths through certain areas of the map by drawing a line across the region as shown below (Zone B).
However, the above method has a few drawbacks: the developer/user has to 1. manually edit the map file and rerun the navigation stack 2. validate whether the added virtual zone is marked correctly or not (editing configurations file) and 3. can’t edit the map on the go as per the warehouse operations requirements.
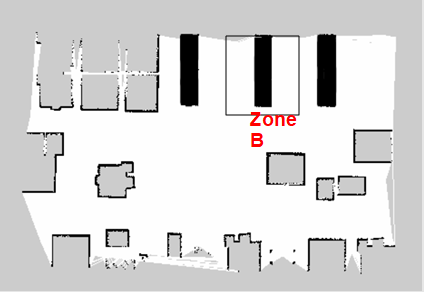
The above method is not efficient from a user point of view and each time a change is required, it has to be done manually by the end-user. To tackle this challenge, we at Ignitarium implemented a virtual fence zone using the custom costmap2D plugins where the user can update the map with the virtual obstacle zone from the Rviz tool. Our approach maps the coordinates value of each mouse click (left or right) or touches event on the map to cell value where we set the cost of the cell as either LETHAL_OBSTACLE or NO_INFORMATION accordingly.
A demo of real-time path planning of a mobile robot influenced by Virtual Fencing can be seen in the below video. Note how the mobile robot maps its path dynamically as the obstacles in its previously planned path keep changing.
This feature can be easily migrated to web-based or smartphone-based applications.
Virtual Fencing is also useful in areas of high traffic which includes other moving vehicles such as fork-lift trucks or autonomous moving machines where the risk of a collision is very high. Also, when the factory workplace requires sanitization (AMRs cannot be deployed in unclean environments as it violates their intended use), virtual fences could be setup around the area until the maintenance work is completed.
Other use cases of Virtual Fencing
The most popular consumer robots which implement and use the virtual fencing feature are lidar based vacuum cleaning robots.
Agricultural farming robots and aerial drones in an outdoor environment rely on global positioning systems (GPS) for marking landmarks in the map for virtually fencing their environments, thus protecting the robot from any collision with humans or from any other dangerous objects.
Conclusion
The next 10 years will be crucial for manufacturing, and an organization’s success will depend on its ability to handle the shift from traditional production to Industry 4.0-style automation. Employee safety must not be overlooked in the enthusiasm of releasing robots from their cages so they may work alongside humans. Although unforeseen dangers are possible even with safety safeguards in place, they may be avoided if workers are adequately taught on the robotic system and the robotic integrator has fulfilled all project requirements, such as appropriate installation, programming, and risk assessment.
Safety in the factory set up is as critical as component preparation or end part quality. Safety as a culture must be established at all levels of a business.
471 thoughts on “Enabling safety in workplaces with mobile robots using Virtual Fencing”
Thank you for your sharing. I am worried that I lack creative ideas. It is your article that makes me full of hope. Thank you. But, I have a question, can you help me? https://accounts.binance.com/sl/register?ref=OMM3XK51
princi b sans ordonnance: PharmaDirecte – achat de viagra
viagra pharmacie sans ordonnance: cialis 20mg prix en pharmacie – mГ©dicaments pour le stress sans ordonnance
medicijn: verzorgingsproducten apotheek – mediceinen
piercing rens apotek: Trygg Med – vond lukt i underlivet apotek
https://zorgpakket.com/# betrouwbare online apotheek zonder recept
https://snabbapoteket.com/# acetylcystein receptfritt apotek
munskydd fГ¶r barn apotek: Snabb Apoteket – l arginin apotek
poppers apotek [url=https://tryggmed.shop/#]Trygg Med[/url] akupunkturnГҐler apotek
mijn medicijnen bestellen: Medicijn Punt – medicijne
http://zorgpakket.com/# mijn medicijnkosten
filmdragerade tabletter: Snabb Apoteket – hГҐltagning apotek
sjekke fГёflekk apotek [url=https://tryggmed.com/#]bomullshansker apotek[/url] ryggstГёtte apotek
medicatie apotheker review: apotheek apotheek – farma online
https://zorgpakket.shop/# online apotheek goedkoper
http://tryggmed.com/# chlamydia test apotek
slankemiddel apotek: TryggMed – tilbud apotek
röd bh [url=https://snabbapoteket.shop/#]aspirin 75 mg apotek[/url] hämta covidtest på apotek
apotek internet: gua sha apotek – apotek nagelsvamp
http://snabbapoteket.com/# jour apotek
apotek ГёyedrГҐper: TryggMed – billig frakt
nett apotek: magnesium l-threonate apotek – sГҐr lim apotek
apotek ombud [url=https://snabbapoteket.shop/#]tabletter med paracetamol[/url] apotek apotek
http://tryggmed.com/# intimvask best i test
https://tryggmed.com/# apoteket norge
e-vitamin olje apotek: TryggMed – e-vitamin olje apotek
apotek glidemiddel: apotek halstabletter – apotek sГёndag
https://zorgpakket.shop/# afbeelding medicijnen
medicijnen online [url=https://zorgpakket.shop/#]farmacia online[/url] online apotheker
salisylsyre krem apotek: Trygg Med – Гёyelapp apotek
medicijn recept: online pharmacy – apotheek online nl
https://zorgpakket.com/# medicijn bestellen apotheek
medicin hemleverans samma dag [url=https://snabbapoteket.shop/#]SnabbApoteket[/url] nagelsvamp apotek
https://zorgpakket.com/# online apotheek recept
online mexico pharmacy USA: viagra pills from mexico – legit mexican pharmacy for hair loss pills
https://medimexicorx.com/# pharmacies in mexico that ship to usa
buy medicines online in india [url=https://indiamedshub.shop/#]Online medicine home delivery[/url] IndiaMedsHub
prescription drugs mexico pharmacy: legit mexico pharmacy shipping to USA – viagra pills from mexico
ultram online pharmacy: mexican pharmacy online percocet – provigil pharmacy online
http://medimexicorx.com/# mexican pharmaceuticals online
http://indiamedshub.com/# india online pharmacy
MediMexicoRx [url=https://medimexicorx.com/#]semaglutide mexico price[/url] best mexican pharmacy online
MediMexicoRx: MediMexicoRx – MediMexicoRx
https://indiamedshub.shop/# reputable indian pharmacies
india pharmacy [url=https://indiamedshub.com/#]mail order pharmacy india[/url] indian pharmacy online
IndiaMedsHub: IndiaMedsHub – mail order pharmacy india
https://expresscarerx.online/# ExpressCareRx
jewel osco pharmacy: viagra pharmacy reviews online – ExpressCareRx
https://expresscarerx.org/# apollo pharmacy online
ExpressCareRx [url=https://expresscarerx.online/#]ExpressCareRx[/url] pharmacy drug store
https://expresscarerx.org/# methylphenidate online pharmacy
buy antibiotics over the counter in mexico: generic drugs mexican pharmacy – accutane mexico buy online
MediMexicoRx: order kamagra from mexican pharmacy – MediMexicoRx
india pharmacy cymbalta [url=https://expresscarerx.online/#]safe online pharmacy cialis[/url] bactrim online pharmacy
http://medimexicorx.com/# MediMexicoRx
pharmacy times: ExpressCareRx – ExpressCareRx
renova mexico pharmacy: optumrx pharmacy – pharmacy viagra now
https://expresscarerx.org/# purchase adipex from an online pharmacy
https://expresscarerx.online/# tamiflu pharmacy
MediMexicoRx [url=http://medimexicorx.com/#]MediMexicoRx[/url] MediMexicoRx
best prices on finasteride in mexico: legit mexico pharmacy shipping to USA – buy meds from mexican pharmacy
cialis online american pharmacy: ExpressCareRx – low cost online pharmacy
http://indiamedshub.com/# top 10 pharmacies in india
buy cheap meds from a mexican pharmacy [url=https://medimexicorx.shop/#]order kamagra from mexican pharmacy[/url] MediMexicoRx
compounding pharmacy viagra: ExpressCareRx – ExpressCareRx
buy prescription drugs from india: IndiaMedsHub – IndiaMedsHub
https://indiamedshub.com/# online pharmacy india
https://medimexicorx.com/# reputable mexican pharmacies online
MediMexicoRx [url=https://medimexicorx.shop/#]buy neurontin in mexico[/url] MediMexicoRx
buy meds from mexican pharmacy: MediMexicoRx – п»їmexican pharmacy
https://medimexicorx.shop/# mexican drugstore online
IndiaMedsHub: Online medicine order – online shopping pharmacy india
IndiaMedsHub [url=https://indiamedshub.com/#]mail order pharmacy india[/url] IndiaMedsHub
venlafaxine xr online pharmacy: ambien pharmacy no prescription – viagra from vipps pharmacy
https://isotretinoinfromcanada.shop/# buy Accutane online
buy Accutane online [url=https://isotretinoinfromcanada.shop/#]purchase generic Accutane online discreetly[/url] isotretinoin online
purchase generic Zoloft online discreetly: sertraline online – purchase generic Zoloft online discreetly
order isotretinoin from Canada to US: order isotretinoin from Canada to US – buy Accutane online
https://zoloft.company/# Zoloft online pharmacy USA
https://lexapro.pro/# lexapro cheapest price
generic Finasteride without prescription [url=https://finasteridefromcanada.shop/#]Finasteride From Canada[/url] Propecia for hair loss online
cheap Accutane: Isotretinoin From Canada – Isotretinoin From Canada
buy lexapro from canada: lexapro pills for sale – Lexapro for depression online
https://lexapro.pro/# lexapro generic
where can i buy generic lexapro: lexapro 20mg – lexapro 10 mg generic
lexapro 20 mg tablet [url=https://lexapro.pro/#]Lexapro for depression online[/url] lexapro 20mg pill
lexapro 2.5 mg: how much is lexapro 10 mg – Lexapro for depression online
https://zoloft.company/# Zoloft for sale
https://tadalafilfromindia.shop/# tadalafil online no rx
Propecia for hair loss online: generic Finasteride without prescription – Propecia for hair loss online
buy Zoloft online [url=https://zoloft.company/#]Zoloft Company[/url] generic sertraline
https://lexapro.pro/# buy lexapro brand name online
lexapro 1.25 mg: lexapro 10mg – lexapro 20mg pill
purchase generic Accutane online discreetly: cheap Accutane – cheap Accutane
https://lexapro.pro/# buy lexapro online without prescription
compare lexapro prices [url=https://lexapro.pro/#]where can you buy lexapro[/url] lexapro tablets australia
generic Finasteride without prescription: generic Finasteride without prescription – generic Finasteride without prescription
https://lexapro.pro/# lexapro generic over the counter
https://zoloft.company/# buy Zoloft online without prescription USA
Propecia for hair loss online: buying generic propecia without insurance – cheap Propecia Canada
lexapro 15mg [url=https://lexapro.pro/#]Lexapro for depression online[/url] lexapro tablets australia
Finasteride From Canada: Propecia for hair loss online – generic Finasteride without prescription
https://lexapro.pro/# buy lexapro online india
propecia brand name: generic Finasteride without prescription – generic Finasteride without prescription
lexapro drug [url=https://lexapro.pro/#]Lexapro for depression online[/url] Lexapro for depression online
Lexapro for depression online: lexapro coupon – lexapro 20 mg tablet
https://zoloft.company/# buy Zoloft online without prescription USA
https://finasteridefromcanada.shop/# order cheap propecia price
Lexapro for depression online: Lexapro for depression online – brand name lexapro from canada
Lexapro for depression online [url=https://lexapro.pro/#]lexapro prescription price[/url] Lexapro for depression online
https://zoloft.company/# purchase generic Zoloft online discreetly
purchase generic Accutane online discreetly: cheap Accutane – buy Accutane online
generic isotretinoin [url=http://isotretinoinfromcanada.com/#]Accutane for sale[/url] isotretinoin online
cheap Zoloft: purchase generic Zoloft online discreetly – cheap Zoloft
https://finasteridefromcanada.shop/# cheap Propecia Canada
http://finasteridefromcanada.com/# Propecia for hair loss online
Cialis without prescription: buy Cialis online cheap – Cialis without prescription
propecia price [url=https://finasteridefromcanada.shop/#]propecia generic[/url] cheap Propecia Canada
can i buy lexapro online without prescription: lexapro 5mg – Lexapro for depression online
https://lexapro.pro/# where can i get lexapro brand medication
Zoloft online pharmacy USA: Zoloft Company – sertraline online
Lexapro for depression online [url=https://lexapro.pro/#]Lexapro for depression online[/url] Lexapro for depression online
https://finasteridefromcanada.shop/# Finasteride From Canada
https://isotretinoinfromcanada.shop/# cheap Accutane
cheap Cialis Canada: buy tadalafil cialis – Cialis without prescription
lexapro 20 [url=https://lexapro.pro/#]Lexapro for depression online[/url] Lexapro for depression online
http://finasteridefromcanada.com/# generic Finasteride without prescription
buy propecia: cheap Propecia Canada – cost generic propecia without a prescription
buy Zoloft online: generic sertraline – Zoloft for sale
Lexapro for depression online [url=https://lexapro.pro/#]Lexapro for depression online[/url] cheapest price for generic lexapro
Accutane for sale: purchase generic Accutane online discreetly – order isotretinoin from Canada to US
cheap Propecia Canada: cost of propecia without prescription – cheap Propecia Canada
https://finasteridefromcanada.com/# Propecia for hair loss online
order isotretinoin from Canada to US [url=https://isotretinoinfromcanada.shop/#]USA-safe Accutane sourcing[/url] USA-safe Accutane sourcing
Lexapro for depression online: Lexapro for depression online – Lexapro for depression online
cheap Propecia Canada: Propecia for hair loss online – Propecia for hair loss online
tadalafil online no rx [url=http://tadalafilfromindia.com/#]buy Cialis online cheap[/url] tadalafil online no rx
order isotretinoin from Canada to US: generic isotretinoin – isotretinoin online
get propecia tablets: generic Finasteride without prescription – generic Finasteride without prescription
http://finasteridefromcanada.com/# Finasteride From Canada
cheap Propecia Canada: Finasteride From Canada – cost generic propecia without a prescription
generic Finasteride without prescription: generic Finasteride without prescription – generic Finasteride without prescription
purchase generic Accutane online discreetly: purchase generic Accutane online discreetly – purchase generic Accutane online discreetly
http://tadalafilfromindia.com/# buy Cialis online cheap
buy Accutane online: USA-safe Accutane sourcing – isotretinoin online
buy Zoloft online without prescription USA: buy Zoloft online without prescription USA – Zoloft Company
buy lexapro online without prescription [url=https://lexapro.pro/#]price for lexapro 10 mg[/url] can you buy lexapro over the counter
ReliefMeds USA: anti-inflammatory steroids online – prednisone 10 mg over the counter
ClearMeds Direct: ClearMeds Direct – antibiotic treatment online no Rx
side effects from gabapentin drug: gabapentin induced diarrhea – NeuroRelief Rx
prednisone best price [url=https://reliefmedsusa.shop/#]order corticosteroids without prescription[/url] can i buy prednisone online in uk
http://clomidhubpharmacy.com/# Clomid Hub Pharmacy
buy prednisone online no script: prednisone 50 mg buy – prednisone 10mg
gabapentin cause anger: NeuroRelief Rx – can i take gabapentin with seroquel
ClearMeds Direct: antibiotic treatment online no Rx – antibiotic treatment online no Rx
zoloft gabapentin interaction [url=https://neuroreliefrx.shop/#]gabapentin dosing information[/url] mixing gabapentin and soma
https://reliefmedsusa.com/# order corticosteroids without prescription
can i buy clomid without a prescription: Clomid Hub Pharmacy – Clomid Hub
affordable Modafinil for cognitive enhancement: WakeMedsRX – nootropic Modafinil shipped to USA
where buy clomid [url=https://clomidhubpharmacy.shop/#]clomid pill[/url] cost of clomid without insurance
cheap prednisone online: Relief Meds USA – buying prednisone without prescription
Clomid Hub: get cheap clomid without rx – can you buy clomid no prescription
prednisone 30 mg daily: order corticosteroids without prescription – Relief Meds USA
gabapentin 400 mg pret [url=https://neuroreliefrx.shop/#]gabapentin mg tablets[/url] fluoxetine tablet
gabapentin price canada: NeuroRelief Rx – NeuroRelief Rx
https://clomidhubpharmacy.com/# Clomid Hub
NeuroRelief Rx: NeuroRelief Rx – gabapentin stada 600 mg nebenwirkungen
Relief Meds USA [url=https://reliefmedsusa.com/#]order corticosteroids without prescription[/url] order corticosteroids without prescription
order corticosteroids without prescription: ReliefMeds USA – anti-inflammatory steroids online
Clomid Hub: Clomid Hub Pharmacy – Clomid Hub Pharmacy
wakefulness medication online no Rx: smart drugs online US pharmacy – Wake Meds RX
buy prednisone tablets uk [url=https://reliefmedsusa.shop/#]ReliefMeds USA[/url] buy prednisone 50 mg
ClearMeds Direct: antibiotic treatment online no Rx – low-cost antibiotics delivered in USA
Clear Meds Direct: ClearMeds Direct – antibiotic treatment online no Rx
https://reliefmedsusa.shop/# prednisone 5084
Clomid Hub [url=https://clomidhubpharmacy.shop/#]cost of clomid for sale[/url] Clomid Hub Pharmacy
order corticosteroids without prescription: order corticosteroids without prescription – anti-inflammatory steroids online
Clear Meds Direct: generic amoxicillin online – ClearMeds Direct
NeuroRelief Rx: efectos secundarios del gabapentin 300 mg – NeuroRelief Rx
can i order clomid tablets [url=https://clomidhubpharmacy.com/#]can you buy clomid for sale[/url] can you get clomid tablets
where to buy prednisone 20mg: anti-inflammatory steroids online – order corticosteroids without prescription
can i buy clomid for sale: Clomid Hub – where buy generic clomid no prescription
can i order clomid pill: Clomid Hub – how to buy cheap clomid tablets
gabapentin toxicity treatment [url=https://neuroreliefrx.shop/#]NeuroRelief Rx[/url] gabapentin pictures 300mg
https://neuroreliefrx.shop/# NeuroRelief Rx
can you get cheap clomid no prescription: Clomid Hub Pharmacy – clomid rx
ReliefMeds USA: order corticosteroids without prescription – ReliefMeds USA
antibiotic treatment online no Rx: order amoxicillin without prescription – order amoxicillin without prescription
gabapentin leukocytosis [url=https://neuroreliefrx.shop/#]can i take xanax and gabapentin[/url] NeuroRelief Rx
gabapentin dosage for babies: NeuroRelief Rx – is gabapentin good for sleep
anti-inflammatory steroids online: 10 mg prednisone – order corticosteroids without prescription
Relief Meds USA: prednisone canada pharmacy – order corticosteroids without prescription
low-cost antibiotics delivered in USA [url=https://clearmedsdirect.shop/#]Clear Meds Direct[/url] Clear Meds Direct
https://reliefmedsusa.shop/# anti-inflammatory steroids online
nootropic Modafinil shipped to USA: WakeMeds RX – wakefulness medication online no Rx
prednisone 10 mg brand name: prednisone cost canada – Relief Meds USA
Relief Meds USA: Relief Meds USA – prednisone 30
order amoxicillin without prescription [url=http://clearmedsdirect.com/#]antibiotic treatment online no Rx[/url] antibiotic treatment online no Rx
are neurontin and gabapentin the same drug: NeuroRelief Rx – gabapentin severe headaches
cortisol prednisone: ReliefMeds USA – ReliefMeds USA
gabapentin abuse in prison populations: order gabapentin online usa – sciatica gabapentin dosage
buy cheap meds from a mexican pharmacy [url=http://mexicarerxhub.com/#]buy antibiotics over the counter in mexico[/url] buy viagra from mexican pharmacy
MexiCare Rx Hub: MexiCare Rx Hub – order azithromycin mexico
https://canadrxnexus.com/# CanadRx Nexus
CanadRx Nexus: canadian pharmacy price checker – CanadRx Nexus
mexico drug stores pharmacies: best mexican online pharmacies – MexiCare Rx Hub
best mail order pharmacy canada [url=https://canadrxnexus.com/#]CanadRx Nexus[/url] reliable canadian pharmacy
CanadRx Nexus: canadian pharmacy uk delivery – CanadRx Nexus
indian pharmacy paypal: online pharmacy india – best online pharmacy india
MexiCare Rx Hub: MexiCare Rx Hub – mexico pharmacies prescription drugs
best prices on finasteride in mexico [url=http://mexicarerxhub.com/#]MexiCare Rx Hub[/url] safe place to buy semaglutide online mexico
medication canadian pharmacy: CanadRx Nexus – CanadRx Nexus
https://canadrxnexus.shop/# CanadRx Nexus
buy modafinil from mexico no rx: order azithromycin mexico – mexican pharmacy for americans
mexico drug stores pharmacies: mexico drug stores pharmacies – buying from online mexican pharmacy
mail order pharmacy india [url=http://indigenixpharm.com/#]IndiGenix Pharmacy[/url] IndiGenix Pharmacy
legit mexican pharmacy for hair loss pills: MexiCare Rx Hub – MexiCare Rx Hub
indian pharmacy: IndiGenix Pharmacy – IndiGenix Pharmacy
MexiCare Rx Hub: MexiCare Rx Hub – best online pharmacies in mexico
MexiCare Rx Hub [url=http://mexicarerxhub.com/#]buy from mexico pharmacy[/url] MexiCare Rx Hub
CanadRx Nexus: canadian pharmacy in canada – pharmacies in canada that ship to the us
http://indigenixpharm.com/# IndiGenix Pharmacy
IndiGenix Pharmacy: IndiGenix Pharmacy – IndiGenix Pharmacy
Online medicine order: indian pharmacies safe – IndiGenix Pharmacy
canadian pharmacies compare [url=https://canadrxnexus.shop/#]CanadRx Nexus[/url] canadian pharmacy no scripts
MexiCare Rx Hub: MexiCare Rx Hub – MexiCare Rx Hub
order from mexican pharmacy online: tadalafil mexico pharmacy – modafinil mexico online
CanadRx Nexus: CanadRx Nexus – CanadRx Nexus
buy antibiotics over the counter in mexico [url=http://mexicarerxhub.com/#]MexiCare Rx Hub[/url] MexiCare Rx Hub
canadian drug pharmacy: canadian drug stores – canadian mail order pharmacy
http://mexicarerxhub.com/# mexican pharmaceuticals online
canadian pharmacy 24h com safe: canadian pharmacy 24h com – CanadRx Nexus
IndiGenix Pharmacy [url=https://indigenixpharm.shop/#]india pharmacy mail order[/url] best online pharmacy india
reliable canadian pharmacy: cheapest pharmacy canada – best online canadian pharmacy
CanadRx Nexus: CanadRx Nexus – canada pharmacy
real canadian pharmacy [url=https://canadrxnexus.shop/#]the canadian pharmacy[/url] adderall canadian pharmacy
IndiGenix Pharmacy: IndiGenix Pharmacy – online pharmacy india
MexiCare Rx Hub: pharmacies in mexico that ship to usa – MexiCare Rx Hub
canadian pharmacy drugs online: CanadRx Nexus – my canadian pharmacy review
https://mexicarerxhub.shop/# MexiCare Rx Hub
generic drugs mexican pharmacy [url=https://mexicarerxhub.shop/#]prescription drugs mexico pharmacy[/url] tadalafil mexico pharmacy
IndiGenix Pharmacy: IndiGenix Pharmacy – IndiGenix Pharmacy
MexiCare Rx Hub: best online pharmacies in mexico – mexican rx online
MexiCare Rx Hub: buy antibiotics over the counter in mexico – buy from mexico pharmacy
IndiGenix Pharmacy [url=https://indigenixpharm.shop/#]pharmacy website india[/url] india pharmacy mail order
IndiGenix Pharmacy: IndiGenix Pharmacy – IndiGenix Pharmacy
CanadRx Nexus: best online canadian pharmacy – canadian pharmacy mall
MexiCare Rx Hub: accutane mexico buy online – prescription drugs mexico pharmacy
IndiGenix Pharmacy [url=https://indigenixpharm.com/#]IndiGenix Pharmacy[/url] п»їlegitimate online pharmacies india
cheapest pharmacy canada: CanadRx Nexus – CanadRx Nexus
CanadRx Nexus: reputable canadian pharmacy – canadian online pharmacy
https://mexicarerxhub.com/# MexiCare Rx Hub
IndiGenix Pharmacy: best online pharmacy india – world pharmacy india
MexiCare Rx Hub [url=https://mexicarerxhub.com/#]MexiCare Rx Hub[/url] order kamagra from mexican pharmacy
Online medicine home delivery: IndiGenix Pharmacy – cheapest online pharmacy india
MexiCare Rx Hub: MexiCare Rx Hub – best online pharmacies in mexico
MexiCare Rx Hub: cheap cialis mexico – mexico pharmacy
IverCare Pharmacy [url=http://ivercarepharmacy.com/#]cost of ivermectin for humans[/url] IverCare Pharmacy
FluidCare Pharmacy: FluidCare Pharmacy – lasix tablet
buy Zanaflex online USA: RelaxMedsUSA – affordable Zanaflex online pharmacy
http://asthmafreepharmacy.com/# AsthmaFree Pharmacy
rybelsus cash price [url=http://glucosmartrx.com/#]semaglutide diet plan[/url] is rybelsus covered by insurance
ivermectin ebay: ivermectin rabbits – ivermectin horse paste for scabies
ivermectin for snakes: stromectol pill for humans – IverCare Pharmacy
where to inject semaglutide in stomach [url=https://glucosmartrx.com/#]semaglutide alternatives[/url] AsthmaFree Pharmacy
lasix: FluidCare Pharmacy – FluidCare Pharmacy
http://relaxmedsusa.com/# prescription-free muscle relaxants
RelaxMeds USA: muscle relaxants online no Rx – Tizanidine tablets shipped to USA
buy furosemide online [url=https://fluidcarepharmacy.shop/#]FluidCare Pharmacy[/url] lasix furosemide
AsthmaFree Pharmacy: ventolin 4mg price – buy ventolin inhaler without prescription
lasix 40mg: FluidCare Pharmacy – FluidCare Pharmacy
ventolin inhalers: ventolin inhaler non prescription – ventolin prices in canada
lasix 100 mg tablet [url=https://fluidcarepharmacy.com/#]furosemida 40 mg[/url] FluidCare Pharmacy
https://asthmafreepharmacy.shop/# AsthmaFree Pharmacy
AsthmaFree Pharmacy: AsthmaFree Pharmacy – ventolin order online without prescription
ivermectin lotion cost [url=https://ivercarepharmacy.com/#]cost of ivermectin pill[/url] ivermectin coronavirus trials
AsthmaFree Pharmacy: AsthmaFree Pharmacy – where can i buy ventolin in uk
AsthmaFree Pharmacy: ventolin online no prescription – ventolin pharmacy singapore
buy Zanaflex online USA [url=https://relaxmedsusa.com/#]order Tizanidine without prescription[/url] Tizanidine 2mg 4mg tablets for sale
ventolin canadian pharmacy: AsthmaFree Pharmacy – AsthmaFree Pharmacy
FluidCare Pharmacy: FluidCare Pharmacy – lasix 40 mg
http://glucosmartrx.com/# AsthmaFree Pharmacy
AsthmaFree Pharmacy [url=https://asthmafreepharmacy.shop/#]AsthmaFree Pharmacy[/url] AsthmaFree Pharmacy
Zanaflex medication fast delivery: prescription-free muscle relaxants – muscle relaxants online no Rx
lasix 40mg [url=https://fluidcarepharmacy.com/#]lasix pills[/url] furosemide 40mg
muscle relaxants online no Rx: trusted pharmacy Zanaflex USA – prescription-free muscle relaxants
ivermectin for covid treatment: IverCare Pharmacy – IverCare Pharmacy
RelaxMeds USA: Tizanidine 2mg 4mg tablets for sale – affordable Zanaflex online pharmacy
AsthmaFree Pharmacy [url=https://asthmafreepharmacy.com/#]AsthmaFree Pharmacy[/url] AsthmaFree Pharmacy
https://asthmafreepharmacy.com/# AsthmaFree Pharmacy
AsthmaFree Pharmacy: AsthmaFree Pharmacy – semaglutide gastroparesis
lasix 40 mg: lasix pills – lasix dosage
semaglutide price [url=http://glucosmartrx.com/#]AsthmaFree Pharmacy[/url] AsthmaFree Pharmacy
RelaxMeds USA: affordable Zanaflex online pharmacy – safe online source for Tizanidine
ventolin 2: where to buy ventolin – AsthmaFree Pharmacy
FluidCare Pharmacy [url=http://fluidcarepharmacy.com/#]lasix dosage[/url] FluidCare Pharmacy
http://glucosmartrx.com/# AsthmaFree Pharmacy
ivermectin injections: IverCare Pharmacy – IverCare Pharmacy
IverCare Pharmacy: ivermectin over the counter – ivermectin alternatives for humans
IverCare Pharmacy: IverCare Pharmacy – IverCare Pharmacy
FluidCare Pharmacy [url=http://fluidcarepharmacy.com/#]FluidCare Pharmacy[/url] FluidCare Pharmacy
Tizanidine 2mg 4mg tablets for sale: safe online source for Tizanidine – cheap muscle relaxer online USA
ventolin online united states: ventolin on line – ventolin capsule
ivermectin for head lice: IverCare Pharmacy – IverCare Pharmacy
Zanaflex medication fast delivery [url=https://relaxmedsusa.shop/#]trusted pharmacy Zanaflex USA[/url] safe online source for Tizanidine
cheap muscle relaxer online USA: relief from muscle spasms online – prescription-free muscle relaxants
affordable Zanaflex online pharmacy: cheap muscle relaxer online USA – relief from muscle spasms online
lasix furosemide [url=https://fluidcarepharmacy.com/#]FluidCare Pharmacy[/url] lasix 40 mg
https://asthmafreepharmacy.com/# generic ventolin price
horse stromectol: IverCare Pharmacy – ivermectin shampoo for head lice
RelaxMeds USA: muscle relaxants online no Rx – RelaxMedsUSA
Tizanidine tablets shipped to USA [url=https://relaxmedsusa.com/#]RelaxMeds USA[/url] trusted pharmacy Zanaflex USA
rybelsus pill form: AsthmaFree Pharmacy – AsthmaFree Pharmacy
FluidCare Pharmacy: FluidCare Pharmacy – lasix for sale
Slot oyunlari Pinco-da: Pinco r?smi sayt – Etibarli onlayn kazino Az?rbaycanda
Yuks?k RTP slotlar [url=https://pinwinaz.pro/#]Pinco kazino[/url] Pinco casino mobil t?tbiq
Jiliko bonus: jilwin – Jiliko slots
Nha cai uy tin Vi?t Nam: Dang ky GK88 – GK88
Swerte99 slots: Swerte99 bonus – Swerte99 bonus
https://swertewin.life/# Swerte99 casino
Bandar togel resmi Indonesia: Link alternatif Abutogel – Situs togel online terpercaya
Swerte99 login [url=https://swertewin.life/#]Swerte99 bonus[/url] Swerte99 login
Link vao GK88 m?i nh?t: Link vao GK88 m?i nh?t – Khuy?n mai GK88
Online gambling platform Jollibet: Jollibet online sabong – jollibet
Jiliko bonus: maglaro ng Jiliko online sa Pilipinas – Jiliko
Abutogel [url=https://abutowin.icu/#]Bandar togel resmi Indonesia[/url] Situs togel online terpercaya
maglaro ng Jiliko online sa Pilipinas: Jiliko slots – Jiliko login
jollibet app: Jollibet online sabong – 1winphili
https://jilwin.pro/# Jiliko
Ðang ký GK88: Casino online GK88 – Nhà cái uy tín Vi?t Nam
Jiliko login: jilwin – Jiliko
Rut ti?n nhanh GK88 [url=https://gkwinviet.company/#]Dang ky GK88[/url] Khuy?n mai GK88
Bandar togel resmi Indonesia: Abutogel login – Abutogel
Jackpot togel hari ini: Bandar togel resmi Indonesia – Abutogel login
Abutogel: Abutogel – Link alternatif Abutogel
Judi online deposit pulsa: Mandiribet login – Situs judi online terpercaya Indonesia
Link alternatif Abutogel [url=https://abutowin.icu/#]Link alternatif Abutogel[/url] Abutogel login
Live casino Mandiribet: Mandiribet – Situs judi resmi berlisensi
https://1winphili.company/# jollibet casino
Abutogel login: Situs togel online terpercaya – Abutogel login
Yeni az?rbaycan kazino sayt?: Pinco r?smi sayt – Kazino bonuslar? 2025 Az?rbaycan
Kazino bonuslar? 2025 Az?rbaycan [url=https://pinwinaz.pro/#]Onlayn rulet v? blackjack[/url] Yeni az?rbaycan kazino sayt?
Canli krupyerl? oyunlar: Pinco casino mobil t?tbiq – Slot oyunlari Pinco-da
Ca cu?c tr?c tuy?n GK88: Tro choi n? hu GK88 – GK88
Yeni az?rbaycan kazino sayt?: Onlayn kazino Az?rbaycan – Etibarl? onlayn kazino Az?rbaycanda
Jollibet online sabong [url=https://1winphili.company/#]Online casino Jollibet Philippines[/url] jollibet
Beta138: Link alternatif Beta138 – Promo slot gacor hari ini
Swerte99 slots: Swerte99 online gaming Pilipinas – Swerte99 casino walang deposit bonus para sa Pinoy
Online gambling platform Jollibet: Online casino Jollibet Philippines – jollibet login
https://swertewin.life/# Swerte99 casino
Slot gacor Beta138: Link alternatif Beta138 – Withdraw cepat Beta138
Pinco r?smi sayt [url=https://pinwinaz.pro/#]Canl? krupyerl? oyunlar[/url] Uduslar? tez c?xar Pinco il?
Online gambling platform Jollibet: Online betting Philippines – jollibet app
Link vao GK88 m?i nh?t: Casino online GK88 – Tro choi n? hu GK88
Online gambling platform Jollibet: jollibet login – Online betting Philippines
Swerte99 casino: Swerte99 casino walang deposit bonus para sa Pinoy – Swerte99 app
Tro choi n? hu GK88: Nha cai uy tin Vi?t Nam – Link vao GK88 m?i nh?t
https://swertewin.life/# Swerte99 casino
Etibarli onlayn kazino Az?rbaycanda: Yüks?k RTP slotlar – Pinco casino mobil t?tbiq
Swerte99 slots: Swerte99 login – Swerte99 bonus
1winphili [url=https://1winphili.company/#]Online betting Philippines[/url] jollibet casino
Live casino Indonesia: Bandar bola resmi – Situs judi resmi berlisensi
indian pharmacy online: top 10 online pharmacy in india – Indian Meds One
tescos pharmacy viagra: pharmacy rx one order status – MediDirect USA
buy cheap meds from a mexican pharmacy: buy cialis from mexico – Mexican Pharmacy Hub
http://medidirectusa.com/# crestor pharmacy online
mail order pharmacy india [url=http://indianmedsone.com/#]Indian Meds One[/url] Indian Meds One
cheap cialis mexico: Mexican Pharmacy Hub – Mexican Pharmacy Hub
best online pharmacies in mexico: Mexican Pharmacy Hub – buying prescription drugs in mexico online
Indian Meds One: online pharmacy india – indian pharmacies safe
MediDirect USA: online pharmacy diflucan – pharmacy rx online
MediDirect USA [url=https://medidirectusa.com/#]MediDirect USA[/url] MediDirect USA
indianpharmacy com: india pharmacy – Indian Meds One
pharmacy ce online: meijer pharmacy store hours – pharmacy coupons
https://medidirectusa.com/# turkish pharmacy online
mail order pharmacy india: online pharmacy india – top online pharmacy india
Mexican Pharmacy Hub [url=https://mexicanpharmacyhub.shop/#]Mexican Pharmacy Hub[/url] rybelsus from mexican pharmacy
MediDirect USA: MediDirect USA – maxalt melt pharmacy
MediDirect USA: MediDirect USA – MediDirect USA
indian pharmacy online: mail order pharmacy india – Indian Meds One
MediDirect USA: compounding pharmacy piroxicam – MediDirect USA
https://medidirectusa.shop/# Lisinopril
safe mexican online pharmacy: Mexican Pharmacy Hub – Mexican Pharmacy Hub
pharmacy website india [url=http://indianmedsone.com/#]Indian Meds One[/url] Indian Meds One
mexican rx online: Mexican Pharmacy Hub – medicine in mexico pharmacies
Indian Meds One: mail order pharmacy india – indianpharmacy com
Mexican Pharmacy Hub: safe place to buy semaglutide online mexico – Mexican Pharmacy Hub
MediDirect USA [url=https://medidirectusa.com/#]MediDirect USA[/url] MediDirect USA
Indian Meds One: Indian Meds One – Indian Meds One
Indian Meds One: Indian Meds One – indian pharmacy
top 10 pharmacies in india: Indian Meds One – Indian Meds One
https://mexicanpharmacyhub.shop/# medication from mexico pharmacy
MediDirect USA: MediDirect USA – MediDirect USA
order medicine online [url=https://medidirectusa.com/#]MediDirect USA[/url] giant food store phoenixville pharmacy
best india pharmacy: Indian Meds One – Indian Meds One
medicine in mexico pharmacies: medication from mexico pharmacy – Mexican Pharmacy Hub
Indian Meds One: indian pharmacy paypal – india pharmacy mail order
indian pharmacy paypal: Indian Meds One – Indian Meds One
Mexican Pharmacy Hub [url=http://mexicanpharmacyhub.com/#]Mexican Pharmacy Hub[/url] Mexican Pharmacy Hub
https://mexicanpharmacyhub.shop/# Mexican Pharmacy Hub
viagra cialis online pharmacy: MediDirect USA – MediDirect USA
Indian Meds One: indian pharmacy – top online pharmacy india
Can you be more specific about the content of your article? After reading it, I still have some doubts. Hope you can help me.
Safe access to generic ED medication [url=http://kamameds.com/#]Men’s sexual health solutions online[/url] Men’s sexual health solutions online
Tadalify: generic cialis from india – Tadalify
Tadalify: buy generic cialis – Tadalify
Tadalify: Tadalify – Tadalify
http://kamameds.com/# KamaMeds
viagra medicine in india: sildenafil generic price – SildenaPeak
cialis shipped from usa: Tadalify – cialis price comparison no prescription
tadalafil soft tabs [url=https://tadalify.shop/#]cialis slogan[/url] what doe cialis look like
Online sources for Kamagra in the United States: Affordable sildenafil citrate tablets for men – Sildenafil oral jelly fast absorption effect
Sildenafil oral jelly fast absorption effect: Kamagra reviews from US customers – Affordable sildenafil citrate tablets for men
Compare Kamagra with branded alternatives: Fast-acting ED solution with discreet packaging – Kamagra oral jelly USA availability
viagra discount online [url=http://sildenapeak.com/#]SildenaPeak[/url] SildenaPeak
https://tadalify.shop/# Tadalify
Non-prescription ED tablets discreetly shipped: KamaMeds – Compare Kamagra with branded alternatives
Tadalify: cialis generico – Tadalify
what possible side effect should a patient taking tadalafil report to a physician quizlet: Tadalify – best time to take cialis
Fast-acting ED solution with discreet packaging: Affordable sildenafil citrate tablets for men – Safe access to generic ED medication
when does cialis go off patent: how well does cialis work – cialis samples for physicians
Safe access to generic ED medication: Kamagra oral jelly USA availability – Sildenafil oral jelly fast absorption effect
viagra for sale [url=http://sildenapeak.com/#]SildenaPeak[/url] SildenaPeak
http://tadalify.com/# Tadalify
Safe access to generic ED medication: KamaMeds – Kamagra reviews from US customers
Online sources for Kamagra in the United States: Fast-acting ED solution with discreet packaging – ED treatment without doctor visits
SildenaPeak: 100mg sildenafil price – SildenaPeak
Online sources for Kamagra in the United States [url=https://kamameds.com/#]Compare Kamagra with branded alternatives[/url] KamaMeds
SildenaPeak: SildenaPeak – female viagra in australia
Tadalify: cialis black 800 to buy in the uk one pill – Tadalify
buying cheap cialis online: Tadalify – Tadalify
https://tadalify.shop/# Tadalify
Tadalify [url=https://tadalify.com/#]cialis picture[/url] Tadalify
Non-prescription ED tablets discreetly shipped: Non-prescription ED tablets discreetly shipped – Fast-acting ED solution with discreet packaging
KamaMeds: Men’s sexual health solutions online – Online sources for Kamagra in the United States
Tadalify: cialis for sale over the counter – who makes cialis
Non-prescription ED tablets discreetly shipped: KamaMeds – Affordable sildenafil citrate tablets for men
Fast-acting ED solution with discreet packaging [url=http://kamameds.com/#]Affordable sildenafil citrate tablets for men[/url] Sildenafil oral jelly fast absorption effect
Tadalify: Tadalify – Tadalify
https://kamameds.com/# Fast-acting ED solution with discreet packaging
Tadalify: Tadalify – what is the active ingredient in cialis
Fast-acting ED solution with discreet packaging: Safe access to generic ED medication – Online sources for Kamagra in the United States
ED treatment without doctor visits: Affordable sildenafil citrate tablets for men – Online sources for Kamagra in the United States
Fast-acting ED solution with discreet packaging [url=http://kamameds.com/#]KamaMeds[/url] ED treatment without doctor visits
viagra without presc: SildenaPeak – how to buy viagra online in usa
Kamagra reviews from US customers: Affordable sildenafil citrate tablets for men – KamaMeds
can you buy female viagra in australia: viagra china – female viagra online purchase in india
https://tadalify.shop/# Tadalify
SildenaPeak [url=https://sildenapeak.com/#]SildenaPeak[/url] Viagra Australia
SildenaPeak: viagra price in us – viagra buy in usa
Affordable sildenafil citrate tablets for men: Kamagra oral jelly USA availability – Online sources for Kamagra in the United States
Online sources for Kamagra in the United States: Kamagra reviews from US customers – Kamagra reviews from US customers
purchase viagra in usa [url=http://sildenapeak.com/#]female viagra pills price[/url] sildenafil soft gel
Tadalify: cialis stopped working – Tadalify
can i buy viagra online in usa: brand viagra for sale – SildenaPeak
what doe cialis look like: Tadalify – best place to buy tadalafil online
https://sildenapeak.com/# SildenaPeak
SildenaPeak [url=https://sildenapeak.shop/#]SildenaPeak[/url] SildenaPeak
SildenaPeak: viagra womens – SildenaPeak
Men’s sexual health solutions online: Kamagra reviews from US customers – Compare Kamagra with branded alternatives
Fast-acting ED solution with discreet packaging: Fast-acting ED solution with discreet packaging – Kamagra oral jelly USA availability
Tadalify: Tadalify – cialis for enlarged prostate
viagra paypal australia: sildenafil 100mg generic mexico – pfizer viagra
Non-prescription ED tablets discreetly shipped [url=https://kamameds.shop/#]KamaMeds[/url] ED treatment without doctor visits
where to buy cialis over the counter: cialis generic overnite shipping – Tadalify
https://sildenapeak.shop/# SildenaPeak
Fast-acting ED solution with discreet packaging: ED treatment without doctor visits – Non-prescription ED tablets discreetly shipped
viagra in india online: SildenaPeak – SildenaPeak
how can you get viagra [url=https://sildenapeak.com/#]SildenaPeak[/url] SildenaPeak
ivermectin dose for dogs: IverGrove – IverGrove
prednisone 50 mg price: prednisone 5443 – prednisone cost 10mg