- Ashwin Joseph
- July 6, 2021
Footwear defect detection using Vision Intelligence Systems
Across global industries, AI-driven computer vision systems are enabling the streamlining of the production process so that the products are compliant with the quality criteria set by the company. This in turn brings in advantages of greater efficiency, lower operational costs while enabling 24/7 production and quicker decision making.
Producing defect-free footwear is not easy. With a variety of defects to be recognized like excessive glue, weak bonds, scuff marks, asymmetry, size, metal contamination and sharp points, the time and effort for manual inspection keeps multiplying. Hence, the need for an automated defect detection system in the footwear industry.
This blog describes an application designed for defect detection in footwear raw materials using TYQ-i, Ignitarium’s Deep Learning based Vision Analytics Platform. The project was executed for one of India’s leading footwear manufacturing companies to cut down on the time taken for quality assurance, thus enhancing productivity and helping to digitise the process. The approach and apparatus took into account considerations like positional variance (placing the object in any alignment), various sizes of raw materials, lighting invariance, etc.
The approach taken by the Ignitarium Engineering team is detailed in subsequent sections:
- Dataset preparation
- Approach to solving the problem
- Labelling
- Training
- Accuracy
- Approach to using the application
- Application Screenshots
- Performance
- Conclusion
Dataset Preparation
In order to train a model, we must start with the appropriate amount of relevant data. For the footwear defect detection project, we were provided a variety of footwear raw materials samples of different types from our client’s production factories all over the country. A large dataset of images was generated by the team at Ignitarium by scanning the raw materials in different alignments. Here are some of the sample raw materials.
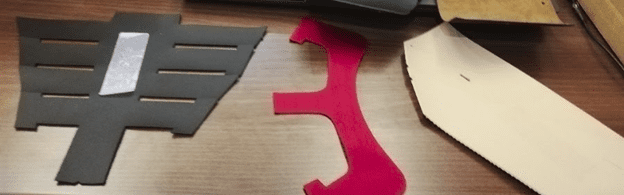
Approach to solving the problem
The approach to solving the problem involved using a combination of various image processing algorithms as well as Deep Learning detection algorithms using a special apparatus designed by Ignitarium. Firstly, using a scanner we were able to retrieve a high resolution colour image of the raw material, then using complex image processing techniques, various preprocessing steps were carried out to ensure positional alignment.
For knowing more about positional alignment, the following links will be quite helpful:
- https://learnopencv.com/image-alignment-ecc-in-opencv-c-python/
- https://opencv-python tutroals.readthedocs.io/en/latest/py_tutorials/py_imgproc/py_geometric_transformations/py_geometric_transformations.html
Deep learning was utilised for the automatic detection of cuts and holes in the raw materials. Semantic segmentation was used for the same and a number of architectures exist for the same like ParseNet, U-Net, etc. The following link will be helpful to gain more insights regarding the same.
U-Net consists of an encoder (downsampler) and decoder (upsampler). In order to learn robust features, and reduce the number of trainable parameters, a pretrained model can be used as the encoder. Thus, the encoder for this task can be a pretrained model like MobileNetV2, whose intermediate outputs will be used, and the decoder will be the upsample block.
Unet Model
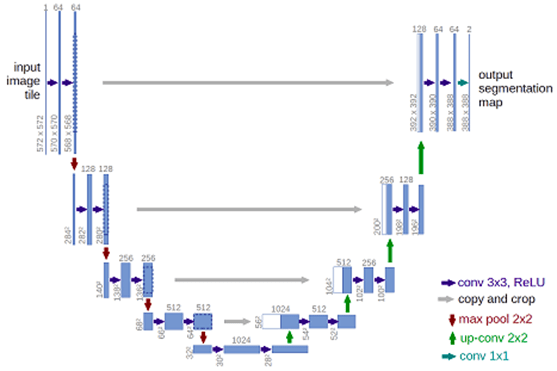
[Source: https://raw.githubusercontent.com/zhixuhao/unet/master/img/u-net-architecture.png]
The following links are helpful for exploring about Unet:
TensorRT optimization
Inorder to speed up the inference results we had carried out TensorRT optimization on our models. TensorRT is an Nvidia software solution for generating optimized models for production deployment of Deep Learning Models. This is achieved by restructuring the graph to perform the operations much faster and more efficiently without changes to the underlying computation in the graph. Detailed information on TensorRT can be found here.
Labelling
Labelling is an important part of any ML-based system. Ignitarium used its own in-house labelling application for the annotation tasks involved in identification of cuts along the footwear raw materials, thus generating the corresponding mask images for the images scanned.
Training
Using the mask images obtained from the inhouse labelling application and the original scan images, training was carried out. Several pretrained encoder-decoder networks like resnet50_segnet, mobilenet_unet, resnet50_unet etc. are available that can be used based on the requirement.
Accuracy
Our custom semantic segmentation network was able to correctly identify the cuts in the raw materials with an accuracy of over 98%.
Approach to using the application
The application requires the user to store templates of each type of raw material they intend to test. It is a one time process for each template. The template creation process involves selecting the positions of holes and drawing the positions of cuts with a mouse pointer as well as marking specific regions that may require custom threshold as compared to other regions as well as entering other details regarding the template like size, article number, left or right orientation etc.
Application Snapshots
Here are some of the snapshots of the application:
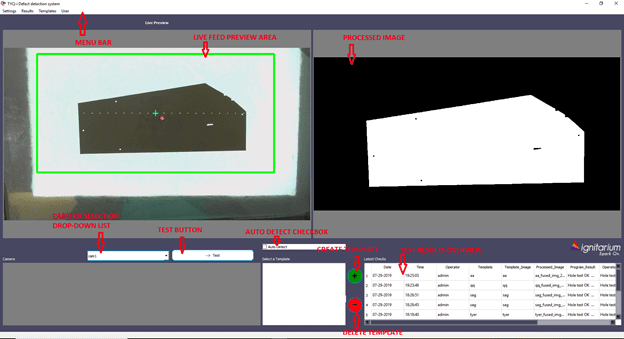
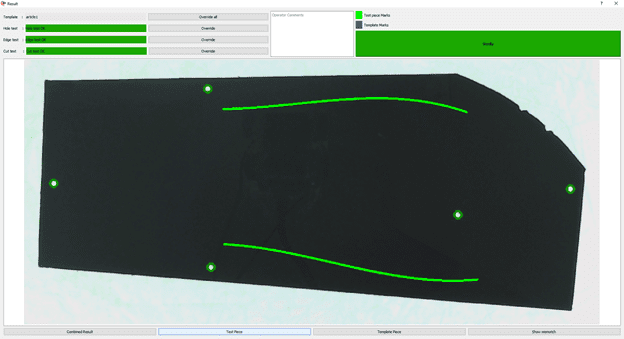
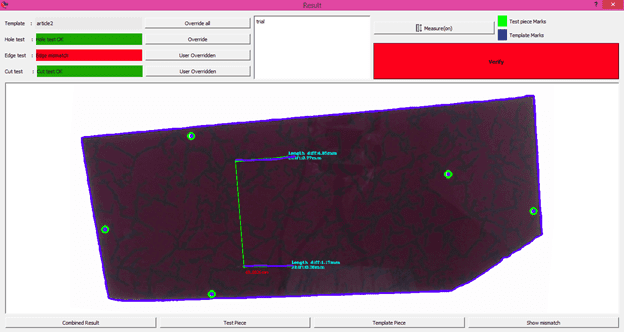
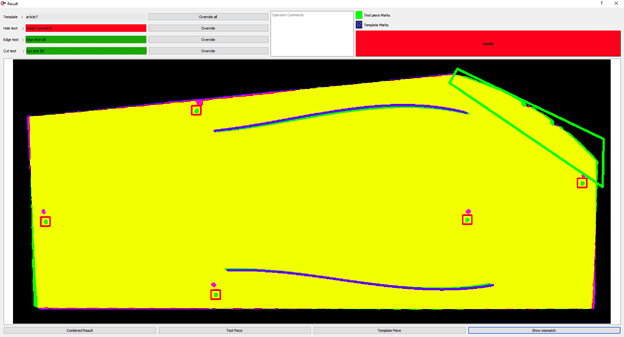
Performance
Scanner’s processing time can vary with resolution used; for the specific scanner used, the total time taken for testing is around 35-40 seconds including scanning and generation of results. Normally the same process when carried out manually by a person, would be highly laborious requiring the verification of dimensions with instruments and visual inspection of raw piece with a template piece, that could take upto 3-4 minutes a piece.
Conclusion
Video explaining the features of the product is available in the following link:
Salient Features of the Footwear Defect Detection Application:
1) Identification of standard defects namely position of holes, cuts as well as outer surface shape of test pieces utilising Deep Learning and Image Processing techniques.
2) Mark custom regions in templates that are to be evaluated against custom tolerance values. Can be utilized in cases where certain regions in the template are to be given more or less prominence.
3) Ability to use CAD files as well as Scanner Feed as Input.
4) Automatic Template Detection feature for identification of corresponding article, if previously stored, thus removing the need for manual selection by the user.
5) Search option for searching for templates based on article names.
6) Folder Structure for neatly organising Article Templates of different sizes
7) Re-orientation of test piece with respect to template either using shape matching or hole position of corresponding template.
8) Availability of different views after testing the Template to make the user understand visually the exact points of defects, if any.
9) Ability to Store and retrieve details from the Result Database regarding tests carried out with various filtering options.
10) Easy modification/ deletion of templates by privileged users.
11) Ability to assign custom privileges to different users of the application like Template Creation/ Modification, Create a new User and Test Analysis Overview.
12) Ability to specify custom tolerance values in the SI metric system for various dimensions taken into consideration for testing for each type of template.
13) Mandate the user to enter certain details like batch number and explanation if results generated by the application were overridden, all which will be stored in the database.
14) Export of report database details into Spreadsheet and PDF formats for Report generation. The details to be included can be controlled using filtering options
15) Ability to Import or Export Template Database.
476 thoughts on “Footwear defect detection using Vision Intelligence Systems”
I don’t think the title of your article matches the content lol. Just kidding, mainly because I had some doubts after reading the article.
purchase levitra canada [url=https://levinevino.com]levitra tab 20mg[/url] vardenafil hcl 10mg
vardenafil 20mg uk levitra online canada levitra buy uk
avoir ordonnance en ligne: PharmaDirecte – secnol sans ordonnance
bГ©quille pharmacie sans ordonnance: PharmaDirecte – pilule jasmine prix
Гёrevoks fjerning apotek [url=http://tryggmed.com/#]Trygg Med[/url] glukose apotek
apotek schampo: Snabb Apoteket – deo till barn
http://zorgpakket.com/# online apotheek recept
fennikel te apotek: homeopati apotek – klГёe i Гёret apotek
http://tryggmed.com/# tisseunderlag apotek
medicatie online bestellen [url=https://zorgpakket.shop/#]Medicijn Punt[/url] online apotheek recept
https://zorgpakket.com/# onlineapotheek
antibiotica kopen zonder recept: MedicijnPunt – viata online apotheek
farmacie medicijn: apteka nl – ons medicatie voor apotheken
https://tryggmed.com/# fordøyelsesenzymer apotek
snabb hГҐruppsГ¤ttning: SnabbApoteket – lГ¤mna in medicin pГҐ apotek
apotek beställa hem [url=https://snabbapoteket.shop/#]SnabbApoteket[/url] apotek på nätet med hemleverans
https://snabbapoteket.com/# apotek chatt
vitamin c apotek: nГ¤tapotek utan recept – apotek ansiktskrГ¤m
https://snabbapoteket.com/# billiga prylar online
bestellen medicijnen: medicijnen kopen online – medicijnen zonder recept
apotek næringsdrikk [url=http://tryggmed.com/#]Trygg Med[/url] apotek +
fiber apotek: Trygg Med – menskopp apotek
https://snabbapoteket.com/# hitta mina recept
online apotek: apotek symbol – alun apotek
mät blodtryck apotek [url=https://snabbapoteket.shop/#]mina tecept[/url] bästa mens appen
mijn medicijn.nl: apotheker medicatie – pharmacy nl
https://snabbapoteket.com/# billiga l-stГ¶d
https://tryggmed.com/# gyldig legitimasjon apotek
klorhexidin apotek: SnabbApoteket – apotek 24 timmar
influensavaksine apotek pris [url=http://tryggmed.com/#]a-vitamin krem apotek[/url] ginkgo biloba apotek
medicijn bestellen apotheek: MedicijnPunt – holland apotheke
http://snabbapoteket.com/# gravid vitaminer bäst i test
apotek Г¶ppet sГ¶ndag: Snabb Apoteket – coronatest pГҐ apotek
nagelsvamp händer bilder [url=https://snabbapoteket.shop/#]snabb leverans apotek[/url] glucosamin apotek
indian pharmacy finasteride: ExpressCareRx – india pharmacy mail order
https://indiamedshub.com/# Online medicine home delivery
https://medimexicorx.shop/# mexican border pharmacies shipping to usa
pharmacy website india: indianpharmacy com – indian pharmacy online
buy cheap meds from a mexican pharmacy [url=https://medimexicorx.com/#]MediMexicoRx[/url] buy cialis from mexico
https://indiamedshub.com/# online shopping pharmacy india
ExpressCareRx: united pharmacy propecia – online pharmacy tetracycline
adipex diet pills online pharmacy: tesco pharmacy viagra price – mail order pharmacy viagra
https://expresscarerx.org/# one rx pharmacy
https://indiamedshub.shop/# IndiaMedsHub
ExpressCareRx [url=http://expresscarerx.org/#]pharmacy shop online[/url] ExpressCareRx
MediMexicoRx: order azithromycin mexico – MediMexicoRx
https://medimexicorx.com/# mexico drug stores pharmacies
ExpressCareRx [url=http://expresscarerx.org/#]viagra pharmacy online[/url] ExpressCareRx
IndiaMedsHub: Online medicine home delivery – IndiaMedsHub
http://expresscarerx.org/# meijer pharmacy free atorvastatin
pharmacy intern drug store: ExpressCareRx – kamagra pharmacy bangkok
https://indiamedshub.shop/# top online pharmacy india
publix pharmacy amoxicillin [url=http://expresscarerx.org/#]ExpressCareRx[/url] ExpressCareRx
ExpressCareRx: ExpressCareRx – rite aid pharmacy store locator
http://medimexicorx.com/# mexican pharmaceuticals online
amoxicillin mexico online pharmacy: buy neurontin in mexico – MediMexicoRx
MediMexicoRx [url=https://medimexicorx.com/#]sildenafil mexico online[/url] trusted mexico pharmacy with US shipping
kaiser pharmacy: abc pharmacy online – bm pharmacy accutane
https://expresscarerx.online/# ExpressCareRx
ExpressCareRx: ExpressCareRx – giant eagle pharmacy
https://expresscarerx.org/# levitra at target pharmacy
low cost mexico pharmacy online [url=https://medimexicorx.com/#]legit mexican pharmacy without prescription[/url] low cost mexico pharmacy online
indian pharmacy: reputable indian online pharmacy – pharmacy website india
https://medimexicorx.com/# buying prescription drugs in mexico
MediMexicoRx: MediMexicoRx – semaglutide mexico price
viagra pharmacy thailand [url=https://expresscarerx.org/#]micardis online pharmacy[/url] online pharmacy ativan no prescription
https://indiamedshub.com/# buy prescription drugs from india
online pharmacy india: cheapest online pharmacy india – IndiaMedsHub
rybelsus from mexican pharmacy: MediMexicoRx – zithromax mexican pharmacy
http://expresscarerx.org/# ExpressCareRx
MediMexicoRx [url=https://medimexicorx.com/#]amoxicillin mexico online pharmacy[/url] safe place to buy semaglutide online mexico
https://indiamedshub.com/# top 10 online pharmacy in india
ExpressCareRx: american pharmacy ambien – mobic online pharmacy
Verapamil [url=http://expresscarerx.org/#]ExpressCareRx[/url] ExpressCareRx
https://indiamedshub.shop/# reputable indian pharmacies
cheap Propecia Canada: Finasteride From Canada – generic Finasteride without prescription
purchase generic Zoloft online discreetly: cheap Zoloft – Zoloft Company
https://zoloft.company/# Zoloft for sale
Finasteride From Canada [url=https://finasteridefromcanada.shop/#]Finasteride From Canada[/url] cheap Propecia Canada
cheap Zoloft: Zoloft for sale – sertraline online
Lexapro for depression online: how much is lexapro 10 mg – how much is lexapro in australia
https://lexapro.pro/# Lexapro for depression online
http://tadalafilfromindia.com/# buy Cialis online cheap
purchase generic Zoloft online discreetly [url=https://zoloft.company/#]cheap Zoloft[/url] Zoloft Company
order isotretinoin from Canada to US: order isotretinoin from Canada to US – Accutane for sale
Lexapro for depression online: Lexapro for depression online – Lexapro for depression online
https://tadalafilfromindia.com/# buy Cialis online cheap
generic isotretinoin [url=https://isotretinoinfromcanada.shop/#]USA-safe Accutane sourcing[/url] purchase generic Accutane online discreetly
lexapro cost australia: buy lexapro without prescription – Lexapro for depression online
sertraline online: generic sertraline – Zoloft online pharmacy USA
https://tadalafilfromindia.com/# Cialis without prescription
https://finasteridefromcanada.com/# generic Finasteride without prescription
cheap Propecia Canada [url=https://finasteridefromcanada.shop/#]generic Finasteride without prescription[/url] Finasteride From Canada
buy Zoloft online without prescription USA: sertraline online – Zoloft Company
Isotretinoin From Canada: USA-safe Accutane sourcing – USA-safe Accutane sourcing
https://tadalafilfromindia.shop/# Tadalafil From India
buy Zoloft online without prescription USA [url=https://zoloft.company/#]cheap Zoloft[/url] Zoloft Company
buy Accutane online: purchase generic Accutane online discreetly – order isotretinoin from Canada to US
https://isotretinoinfromcanada.com/# order isotretinoin from Canada to US
generic sertraline: generic sertraline – Zoloft online pharmacy USA
http://isotretinoinfromcanada.com/# Accutane for sale
sertraline online: cheap Zoloft – cheap Zoloft
Lexapro for depression online [url=https://lexapro.pro/#]Lexapro for depression online[/url] Lexapro for depression online
https://finasteridefromcanada.shop/# cheap Propecia Canada
buy Cialis online cheap: Tadalafil From India – tadalafil online no rx
generic sertraline [url=https://zoloft.company/#]purchase generic Zoloft online discreetly[/url] sertraline online
https://zoloft.company/# Zoloft Company
sertraline online: Zoloft for sale – cheap Zoloft
https://isotretinoinfromcanada.com/# buy Accutane online
cheap Zoloft: cheap Zoloft – buy Zoloft online without prescription USA
purchase generic Zoloft online discreetly [url=https://zoloft.company/#]Zoloft online pharmacy USA[/url] Zoloft Company
https://finasteridefromcanada.shop/# generic Finasteride without prescription
buy Cialis online cheap: generic Cialis from India – cheap Cialis Canada
buy generic lexapro online: lexapro generic 20 mg – lexapro brand name discount
https://isotretinoinfromcanada.shop/# USA-safe Accutane sourcing
cost generic propecia price [url=http://finasteridefromcanada.com/#]generic Finasteride without prescription[/url] Propecia for hair loss online
Zoloft online pharmacy USA: purchase generic Zoloft online discreetly – Zoloft online pharmacy USA
http://isotretinoinfromcanada.com/# Accutane for sale
https://finasteridefromcanada.shop/# Propecia for hair loss online
generic sertraline [url=https://zoloft.company/#]buy Zoloft online without prescription USA[/url] sertraline online
cheap Zoloft: Zoloft for sale – buy Zoloft online without prescription USA
http://finasteridefromcanada.com/# cheap Propecia Canada
generic Finasteride without prescription: generic Finasteride without prescription – Finasteride From Canada
buy Zoloft online [url=https://zoloft.company/#]Zoloft for sale[/url] Zoloft online pharmacy USA
http://tadalafilfromindia.com/# generic Cialis from India
https://lexapro.pro/# Lexapro for depression online
Zoloft online pharmacy USA: buy Zoloft online without prescription USA – buy Zoloft online
Finasteride From Canada [url=https://finasteridefromcanada.shop/#]generic Finasteride without prescription[/url] generic Finasteride without prescription
Isotretinoin From Canada: buy Accutane online – Accutane for sale
buy Cialis online cheap [url=https://tadalafilfromindia.shop/#]buy Cialis online cheap[/url] tadalafil online no rx
USA-safe Accutane sourcing: isotretinoin online – order isotretinoin from Canada to US
Propecia for hair loss online: Finasteride From Canada – cost of generic propecia price
http://tadalafilfromindia.com/# cheap Cialis Canada
Lexapro for depression online [url=https://lexapro.pro/#]Lexapro for depression online[/url] Lexapro for depression online
Tadalafil From India: cheap Cialis Canada – buy Cialis online cheap
order isotretinoin from Canada to US: order isotretinoin from Canada to US – Isotretinoin From Canada
Cialis without prescription: tadalafil online no rx – buy tadalafil india
Lexapro for depression online: Lexapro for depression online – lexapro generic over the counter
https://lexapro.pro/# generic lexapro canada pharmacy
Lexapro for depression online: Lexapro for depression online – lexapro 10 mg tablet
tadalafil online no rx: generic Cialis from India – tadalafil online no rx
http://isotretinoinfromcanada.com/# USA-safe Accutane sourcing
lexapro 1.25 mg: generic brand for lexapro – buy lexapro online india
order Provigil without prescription [url=http://wakemedsrx.com/#]buy Modafinil online USA[/url] safe Provigil online delivery service
Modafinil for focus and productivity: WakeMedsRX – wakefulness medication online no Rx
how to buy prednisone online: prednisone 300mg – ReliefMeds USA
prednisone online india: cheapest prednisone no prescription – anti-inflammatory steroids online
WakeMeds RX: nootropic Modafinil shipped to USA – Wake Meds RX
WakeMedsRX [url=https://wakemedsrx.shop/#]WakeMedsRX[/url] WakeMedsRX
https://clomidhubpharmacy.com/# Clomid Hub Pharmacy
NeuroRelief Rx: buying gabapentin – NeuroRelief Rx
anti-inflammatory steroids online: Relief Meds USA – order corticosteroids without prescription
order corticosteroids without prescription: anti-inflammatory steroids online – ReliefMeds USA
WakeMeds RX [url=http://wakemedsrx.com/#]wakefulness medication online no Rx[/url] nootropic Modafinil shipped to USA
gabapentin 100mg capsules pictures: NeuroRelief Rx – gabapentin 300 mg uses side effect
http://clomidhubpharmacy.com/# how can i get cheap clomid price
NeuroRelief Rx: NeuroRelief Rx – NeuroRelief Rx
smart drugs online US pharmacy [url=https://wakemedsrx.shop/#]Wake Meds RX[/url] where to buy Modafinil legally in the US
buy Modafinil online USA: Modafinil for focus and productivity – smart drugs online US pharmacy
affordable Modafinil for cognitive enhancement: Wake Meds RX – affordable Modafinil for cognitive enhancement
anti-inflammatory steroids online: prednisone 20mg tab price – ReliefMeds USA
Clomid Hub [url=https://clomidhubpharmacy.com/#]buying generic clomid without dr prescription[/url] buy generic clomid without dr prescription
https://reliefmedsusa.shop/# ReliefMeds USA
order corticosteroids without prescription: prednisone generic cost – order corticosteroids without prescription
amoxicillin brand name: can you buy amoxicillin over the counter canada – amoxicillin without a prescription
can you take gabapentin with clonazepam [url=http://neuroreliefrx.com/#]gabapentin and divalproex[/url] NeuroRelief Rx
Clomid Hub Pharmacy: Clomid Hub Pharmacy – Clomid Hub
NeuroRelief Rx: https://gabapentin24h.top – first time gabapentin high
Relief Meds USA [url=https://reliefmedsusa.shop/#]Relief Meds USA[/url] Relief Meds USA
prednisone 5mg over the counter: ReliefMeds USA – order corticosteroids without prescription
gabapentin capsules 300 mg: sodium valproate and gabapentin interaction – conversion from gabapentin to lyrica
ReliefMeds USA: ReliefMeds USA – buy prednisone 1 mg mexico
http://neuroreliefrx.com/# can you buy fluoxetine
order corticosteroids without prescription [url=https://reliefmedsusa.shop/#]order corticosteroids without prescription[/url] prednisone 20mg
gabapentin 600 mg side effcets: gabapentin 1a pharma 100 mg kapseln – NeuroRelief Rx
safe Provigil online delivery service: Wake Meds RX – affordable Modafinil for cognitive enhancement
prednisone 5 mg: anti-inflammatory steroids online – Relief Meds USA
buy prednisone 10mg online [url=https://reliefmedsusa.shop/#]order corticosteroids without prescription[/url] Relief Meds USA
ClearMeds Direct: order amoxicillin without prescription – ClearMeds Direct
Relief Meds USA: prednisone 5 mg tablet cost – order corticosteroids without prescription
ReliefMeds USA: prednisone prescription online – prednisone 10mg prices
amoxicillin 250 mg price in india [url=https://clearmedsdirect.shop/#]low-cost antibiotics delivered in USA[/url] low-cost antibiotics delivered in USA
https://wakemedsrx.com/# buy Modafinil online USA
order corticosteroids without prescription: anti-inflammatory steroids online – can i buy prednisone from canada without a script
order amoxicillin without prescription: amoxicillin 500mg buy online uk – Clear Meds Direct
Relief Meds USA: ReliefMeds USA – order corticosteroids without prescription
Modafinil for ADHD and narcolepsy [url=http://wakemedsrx.com/#]safe Provigil online delivery service[/url] nootropic Modafinil shipped to USA
prednisone 10mg canada: Relief Meds USA – order corticosteroids without prescription
wakefulness medication online no Rx: Wake Meds RX – smart drugs online US pharmacy
ReliefMeds USA: buy prednisone 1 mg mexico – Relief Meds USA
buy Modafinil online USA [url=http://wakemedsrx.com/#]Modafinil for focus and productivity[/url] buy Modafinil online USA
https://clomidhubpharmacy.com/# Clomid Hub Pharmacy
Modafinil for focus and productivity: Wake Meds RX – smart drugs online US pharmacy
prednisone without prescription medication: 5mg prednisone – ReliefMeds USA
Relief Meds USA: Relief Meds USA – prednisone 10 tablet
can you get clomid without insurance [url=https://clomidhubpharmacy.com/#]can i get cheap clomid no prescription[/url] where can i buy generic clomid without dr prescription
low-cost antibiotics delivered in USA: antibiotic treatment online no Rx – Clear Meds Direct
CanadRx Nexus: CanadRx Nexus – CanadRx Nexus
best online pharmacy india [url=http://indigenixpharm.com/#]IndiGenix Pharmacy[/url] п»їlegitimate online pharmacies india
https://canadrxnexus.com/# CanadRx Nexus
MexiCare Rx Hub: MexiCare Rx Hub – MexiCare Rx Hub
my canadian pharmacy: canada pharmacy 24h – online canadian pharmacy
buy neurontin in mexico: order from mexican pharmacy online – MexiCare Rx Hub
MexiCare Rx Hub [url=https://mexicarerxhub.shop/#]best mexican pharmacy online[/url] trusted mexican pharmacy
reputable indian online pharmacy: IndiGenix Pharmacy – IndiGenix Pharmacy
indian pharmacy: best online pharmacy india – IndiGenix Pharmacy
MexiCare Rx Hub [url=https://mexicarerxhub.com/#]MexiCare Rx Hub[/url] low cost mexico pharmacy online
canada rx pharmacy world: CanadRx Nexus – CanadRx Nexus
CanadRx Nexus: CanadRx Nexus – best canadian online pharmacy
https://indigenixpharm.com/# IndiGenix Pharmacy
medication from mexico pharmacy: mexican border pharmacies shipping to usa – MexiCare Rx Hub
canadian drug stores [url=https://canadrxnexus.shop/#]canadian neighbor pharmacy[/url] CanadRx Nexus
CanadRx Nexus: CanadRx Nexus – canadian pharmacy tampa
order from mexican pharmacy online: MexiCare Rx Hub – accutane mexico buy online
IndiGenix Pharmacy: reputable indian pharmacies – IndiGenix Pharmacy
buy from mexico pharmacy [url=https://mexicarerxhub.com/#]MexiCare Rx Hub[/url] MexiCare Rx Hub
MexiCare Rx Hub: MexiCare Rx Hub – modafinil mexico online
CanadRx Nexus: best canadian pharmacy – CanadRx Nexus
https://indigenixpharm.shop/# online pharmacy india
CanadRx Nexus: canadian discount pharmacy – CanadRx Nexus
CanadRx Nexus [url=https://canadrxnexus.com/#]canadian pharmacy com[/url] CanadRx Nexus
canada drugstore pharmacy rx: CanadRx Nexus – canadian pharmacy meds
safe mexican online pharmacy: low cost mexico pharmacy online – MexiCare Rx Hub
IndiGenix Pharmacy: legitimate online pharmacies india – IndiGenix Pharmacy
MexiCare Rx Hub [url=https://mexicarerxhub.shop/#]MexiCare Rx Hub[/url] MexiCare Rx Hub
canadian drugs pharmacy: canada drug pharmacy – canadian mail order pharmacy
http://mexicarerxhub.com/# MexiCare Rx Hub
mexican rx online: best online pharmacies in mexico – MexiCare Rx Hub
Online medicine home delivery [url=http://indigenixpharm.com/#]buy medicines online in india[/url] buy prescription drugs from india
reputable indian online pharmacy: reputable indian pharmacies – п»їlegitimate online pharmacies india
buy cheap meds from a mexican pharmacy: legit mexican pharmacy for hair loss pills – tadalafil mexico pharmacy
Thanks for sharing. I read many of your blog posts, cool, your blog is very good.
mexico drug stores pharmacies: buying from online mexican pharmacy – mexican drugstore online
CanadRx Nexus [url=http://canadrxnexus.com/#]safe canadian pharmacy[/url] CanadRx Nexus
safe online pharmacies in canada: CanadRx Nexus – canadian pharmacy checker
CanadRx Nexus: pharmacy rx world canada – CanadRx Nexus
amoxicillin mexico online pharmacy [url=https://mexicarerxhub.com/#]MexiCare Rx Hub[/url] MexiCare Rx Hub
pharmacy in canada: CanadRx Nexus – best online canadian pharmacy
https://canadrxnexus.com/# CanadRx Nexus
buy prescription drugs from india: top 10 pharmacies in india – IndiGenix Pharmacy
IndiGenix Pharmacy: IndiGenix Pharmacy – IndiGenix Pharmacy
onlinecanadianpharmacy 24 [url=https://canadrxnexus.shop/#]CanadRx Nexus[/url] canadian pharmacy king reviews
IndiGenix Pharmacy: IndiGenix Pharmacy – IndiGenix Pharmacy
MexiCare Rx Hub: MexiCare Rx Hub – MexiCare Rx Hub
MexiCare Rx Hub: MexiCare Rx Hub – trusted mexican pharmacy
canadian pharmacy king reviews [url=https://canadrxnexus.shop/#]CanadRx Nexus[/url] canadian pharmacy ltd
india pharmacy mail order: online pharmacy india – IndiGenix Pharmacy
https://indigenixpharm.com/# top 10 online pharmacy in india
pet meds without vet prescription canada: CanadRx Nexus – global pharmacy canada
CanadRx Nexus: CanadRx Nexus – canada drugs online review
modafinil mexico online [url=https://mexicarerxhub.com/#]MexiCare Rx Hub[/url] order kamagra from mexican pharmacy
MexiCare Rx Hub: MexiCare Rx Hub – MexiCare Rx Hub
AsthmaFree Pharmacy: AsthmaFree Pharmacy – AsthmaFree Pharmacy
relief from muscle spasms online [url=http://relaxmedsusa.com/#]relief from muscle spasms online[/url] Tizanidine tablets shipped to USA
ivermectin for scabies: ivermectin headache – is ivermectin safe for pregnant goats
where to buy stromectol: fleet farm ivermectin – ivermectin apple paste
https://relaxmedsusa.com/# order Tizanidine without prescription
ventolin script [url=http://asthmafreepharmacy.com/#]buy ventolin over the counter[/url] ventolin price
IverCare Pharmacy: IverCare Pharmacy – IverCare Pharmacy
can you buy ventolin over the counter australia: AsthmaFree Pharmacy – AsthmaFree Pharmacy
AsthmaFree Pharmacy [url=https://glucosmartrx.shop/#]AsthmaFree Pharmacy[/url] rybelsus 14 mg weight loss reviews
AsthmaFree Pharmacy: weight loss pills rybelsus – him and hers semaglutide
AsthmaFree Pharmacy: AsthmaFree Pharmacy – can i buy ventolin over the counter in canada
order Tizanidine without prescription: cheap muscle relaxer online USA – prescription-free muscle relaxants
https://glucosmartrx.com/# AsthmaFree Pharmacy
ivermectin covid treatment [url=http://ivercarepharmacy.com/#]IverCare Pharmacy[/url] IverCare Pharmacy
rybelsus 3 mg weight loss: what does semaglutide do to your body – AsthmaFree Pharmacy
rybelsus symptoms [url=https://glucosmartrx.shop/#]AsthmaFree Pharmacy[/url] AsthmaFree Pharmacy
FluidCare Pharmacy: FluidCare Pharmacy – generic lasix
microdosing semaglutide for inflammation: AsthmaFree Pharmacy – AsthmaFree Pharmacy
https://relaxmedsusa.com/# safe online source for Tizanidine
edenbridge pharmaceuticals ivermectin [url=https://ivercarepharmacy.shop/#]IverCare Pharmacy[/url] ivermectin lawsuit
AsthmaFree Pharmacy: ventolin sale uk – AsthmaFree Pharmacy
cheap muscle relaxer online USA: trusted pharmacy Zanaflex USA – cheap muscle relaxer online USA
can you take ibuprofen with rybelsus: AsthmaFree Pharmacy – what are the side effects of rybelsus 3 mg
where to buy ivermectin for guinea pigs [url=https://ivercarepharmacy.com/#]ivermectin lotion cost[/url] IverCare Pharmacy
safe online source for Tizanidine: trusted pharmacy Zanaflex USA – cheap muscle relaxer online USA
AsthmaFree Pharmacy [url=http://glucosmartrx.com/#]AsthmaFree Pharmacy[/url] AsthmaFree Pharmacy
https://fluidcarepharmacy.com/# FluidCare Pharmacy
FluidCare Pharmacy: FluidCare Pharmacy – lasix side effects
AsthmaFree Pharmacy: AsthmaFree Pharmacy – buy ventolin without prescription
RelaxMeds USA [url=https://relaxmedsusa.com/#]safe online source for Tizanidine[/url] prescription-free muscle relaxants
AsthmaFree Pharmacy: does rybelsus cause depression – AsthmaFree Pharmacy
prescription-free muscle relaxants [url=https://relaxmedsusa.com/#]cheap muscle relaxer online USA[/url] buy Zanaflex online USA
https://asthmafreepharmacy.com/# ventolin otc nz
order Tizanidine without prescription: buy Zanaflex online USA – Tizanidine tablets shipped to USA
FluidCare Pharmacy: FluidCare Pharmacy – lasix 100 mg tablet
FluidCare Pharmacy [url=http://fluidcarepharmacy.com/#]furosemide 100 mg[/url] furosemide 40mg
generic lasix: furosemide 40 mg – lasix medication
safe online source for Tizanidine: prescription-free muscle relaxants – Tizanidine 2mg 4mg tablets for sale
AsthmaFree Pharmacy [url=http://glucosmartrx.com/#]compounded semaglutide side effects[/url] semaglutide vs mounjaro
muscle relaxants online no Rx: buy Zanaflex online USA – order Tizanidine without prescription
https://relaxmedsusa.shop/# Zanaflex medication fast delivery
safe online source for Tizanidine: muscle relaxants online no Rx – Zanaflex medication fast delivery
AsthmaFree Pharmacy: buy cheap ventolin – AsthmaFree Pharmacy
furosemide [url=http://fluidcarepharmacy.com/#]FluidCare Pharmacy[/url] lasix 20 mg
ivermectin for coronavirus: ivermectin shampoo – IverCare Pharmacy
ivermectin tablets usp: IverCare Pharmacy – ivermectin for cattle
FluidCare Pharmacy: lasix generic – lasix tablet
FluidCare Pharmacy [url=http://fluidcarepharmacy.com/#]FluidCare Pharmacy[/url] FluidCare Pharmacy
ivermectin walgreens: ivermectin tablet 12mg – ivermectin pills
Tizanidine tablets shipped to USA [url=https://relaxmedsusa.com/#]Tizanidine tablets shipped to USA[/url] order Tizanidine without prescription
order Tizanidine without prescription: order Tizanidine without prescription – Tizanidine tablets shipped to USA
https://ivercarepharmacy.shop/# ivermectin cream cost
buy lasix online: lasix furosemide – FluidCare Pharmacy
AsthmaFree Pharmacy [url=https://glucosmartrx.com/#]semaglutide and hair loss[/url] starting semaglutide
IverCare Pharmacy: IverCare Pharmacy – ivermectin guinea pigs
AsthmaFree Pharmacy: ventolin tablets – AsthmaFree Pharmacy
Slot gacor Beta138: Withdraw cepat Beta138 – Login Beta138
https://jilwin.pro/# Jiliko bonus
Swerte99 [url=https://swertewin.life/#]Swerte99 casino walang deposit bonus para sa Pinoy[/url] Swerte99 casino walang deposit bonus para sa Pinoy
Jiliko login: Jiliko app – Jiliko slots
Online casino Jollibet Philippines: jollibet casino – jollibet login
Bonus new member 100% Mandiribet: Slot gacor hari ini – Situs judi resmi berlisensi
Abutogel: Abutogel login – Jackpot togel hari ini
Situs togel online terpercaya [url=https://abutowin.icu/#]Situs togel online terpercaya[/url] Abutogel login
Judi online deposit pulsa: Situs judi online terpercaya Indonesia – Situs judi resmi berlisensi
https://mandiwinindo.site/# Mandiribet
Jiliko casino walang deposit bonus para sa Pinoy: Jiliko casino walang deposit bonus para sa Pinoy – Jiliko slots
Situs togel online terpercaya: Abutogel – Link alternatif Abutogel
Swerte99 casino [url=https://swertewin.life/#]Swerte99 bonus[/url] Swerte99 casino walang deposit bonus para sa Pinoy
Pinco r?smi sayt: Slot oyunlar? Pinco-da – Slot oyunlar? Pinco-da
Swerte99 app: Swerte99 casino walang deposit bonus para sa Pinoy – Swerte99 login
Bonus new member 100% Mandiribet: Mandiribet – Slot jackpot terbesar Indonesia
Slot oyunlar? Pinco-da [url=https://pinwinaz.pro/#]Slot oyunlar? Pinco-da[/url] Onlayn rulet v? blackjack
1winphili: Online gambling platform Jollibet – Online casino Jollibet Philippines
Swerte99 casino walang deposit bonus para sa Pinoy: Swerte99 login – Swerte99 slots
https://gkwinviet.company/# Slot game d?i thu?ng
Jiliko: Jiliko bonus – Jiliko login
Slot jackpot terbesar Indonesia [url=https://mandiwinindo.site/#]Bonus new member 100% Mandiribet[/url] Situs judi online terpercaya Indonesia
Slot oyunlar? Pinco-da: Yeni az?rbaycan kazino sayt? – Pinco r?smi sayt
Abutogel: Link alternatif Abutogel – Abutogel
Jiliko app: Jiliko app – Jiliko bonus
jollibet: Jollibet online sabong – jollibet login
Jiliko casino [url=https://jilwin.pro/#]maglaro ng Jiliko online sa Pilipinas[/url] jilwin
https://jilwin.pro/# Jiliko casino
Jollibet online sabong: 1winphili – jollibet casino
jollibet casino: Online betting Philippines – jollibet app
Jiliko: Jiliko login – jilwin
Slot jackpot terbesar Indonesia [url=https://mandiwinindo.site/#]Mandiribet[/url] Link alternatif Mandiribet
Pinco casino mobil t?tbiq: Onlayn kazino Az?rbaycan – Yüks?k RTP slotlar
Jiliko app: Jiliko slots – Jiliko casino
jollibet app: Online betting Philippines – jollibet app
Swerte99 casino walang deposit bonus para sa Pinoy [url=https://swertewin.life/#]Swerte99 casino[/url] Swerte99 bonus
jollibet login: jollibet casino – Online betting Philippines
Bandar bola resmi: Live casino Indonesia – Bandar bola resmi
Online casino Jollibet Philippines: jollibet casino – jollibet app
https://1winphili.company/# Jollibet online sabong
GK88 [url=https://gkwinviet.company/#]Ca cu?c tr?c tuy?n GK88[/url] Casino online GK88
Online betting Philippines: jollibet – Online casino Jollibet Philippines
Qeydiyyat bonusu Pinco casino: Onlayn kazino Az?rbaycan – Etibarl? onlayn kazino Az?rbaycanda
Swerte99 casino: Swerte99 casino walang deposit bonus para sa Pinoy – Swerte99 app
Mandiribet: Mandiribet login – Slot jackpot terbesar Indonesia
finasteride mexico pharmacy [url=https://mexicanpharmacyhub.com/#]Mexican Pharmacy Hub[/url] get viagra without prescription from mexico
best india pharmacy: Indian Meds One – Indian Meds One
https://mexicanpharmacyhub.shop/# reputable mexican pharmacies online
australia pharmacy viagra: good online pharmacy – online pharmacy scams
Aebgkeymn: MediDirect USA – israel pharmacy online
Indian Meds One: top 10 pharmacies in india – Indian Meds One
mexico drug stores pharmacies: Mexican Pharmacy Hub – Mexican Pharmacy Hub
river pharmacy revia [url=https://medidirectusa.shop/#]MediDirect USA[/url] dysfunction
MediDirect USA: generic valtrex online pharmacy – MediDirect USA
https://medidirectusa.shop/# wegmans pharmacy
MediDirect USA: MediDirect USA – watson pharmacy viagra
world pharmacy india: best online pharmacy india – reputable indian pharmacies
buy cheap meds from a mexican pharmacy: Mexican Pharmacy Hub – order kamagra from mexican pharmacy
MediDirect USA [url=https://medidirectusa.com/#]MediDirect USA[/url] MediDirect USA
Mexican Pharmacy Hub: Mexican Pharmacy Hub – Mexican Pharmacy Hub
Indian Meds One: legitimate online pharmacies india – Indian Meds One
online shopping pharmacy india: indian pharmacy paypal – indian pharmacy paypal
https://mexicanpharmacyhub.com/# Mexican Pharmacy Hub
Indian Meds One [url=http://indianmedsone.com/#]Indian Meds One[/url] Indian Meds One
best mexican online pharmacies: medicine in mexico pharmacies – mexico drug stores pharmacies
Mexican Pharmacy Hub: buy from mexico pharmacy – legit mexican pharmacy for hair loss pills
top 10 pharmacies in india: Indian Meds One – india online pharmacy
mexican pharmaceuticals online: Mexican Pharmacy Hub – mexican online pharmacies prescription drugs
pharmacy website india: Indian Meds One – Indian Meds One
trusted mexican pharmacy: Mexican Pharmacy Hub – Mexican Pharmacy Hub
MediDirect USA [url=http://medidirectusa.com/#]MediDirect USA[/url] MediDirect USA
cialis tesco pharmacy: MediDirect USA – MediDirect USA
http://indianmedsone.com/# Indian Meds One
pharmacy rx one viagra: people’s pharmacy celebrex – online pharmacy with doctor consultation
MediDirect USA: best pharmacy to buy cialis – brand cialis online pharmacy
buy neurontin in mexico [url=http://mexicanpharmacyhub.com/#]Mexican Pharmacy Hub[/url] buy antibiotics over the counter in mexico
Mexican Pharmacy Hub: Mexican Pharmacy Hub – mexican pharmaceuticals online
buy prescription drugs from india: Indian Meds One – online pharmacy india
amoxicillin mexico online pharmacy: Mexican Pharmacy Hub – Mexican Pharmacy Hub
Indian Meds One [url=http://indianmedsone.com/#]online pharmacy india[/url] Indian Meds One
sams club pharmacy propecia: spanish pharmacy viagra – order viagra online pharmacy
zithromax mexican pharmacy: modafinil mexico online – Mexican Pharmacy Hub
Indian Meds One: Indian Meds One – india pharmacy
https://mexicanpharmacyhub.shop/# mexican drugstore online
MediDirect USA: MediDirect USA – alliance rx specialty pharmacy
indianpharmacy com: online shopping pharmacy india – Indian Meds One
top online pharmacy india [url=https://indianmedsone.com/#]п»їlegitimate online pharmacies india[/url] Indian Meds One
Precose: MediDirect USA – sam’s club pharmacy viagra price
antibiotics online pharmacy: MediDirect USA – MediDirect USA
MediDirect USA: online pharmacy denmark – MediDirect USA
SildenaPeak: how to get viagra prescription – online viagra united states
http://sildenapeak.com/# SildenaPeak
SildenaPeak [url=http://sildenapeak.com/#]sildenafil 100mg price canada[/url] SildenaPeak
KamaMeds: Compare Kamagra with branded alternatives – Men’s sexual health solutions online
Compare Kamagra with branded alternatives: Men’s sexual health solutions online – Kamagra reviews from US customers
buy cialis generic online 10 mg: cialis slogan – purchase cialis online cheap
cialis stopped working: Tadalify – Tadalify
SildenaPeak [url=http://sildenapeak.com/#]cheap generic viagra online canada[/url] SildenaPeak
Tadalify: cialis where to buy in las vegas nv – cialis vs sildenafil
https://kamameds.shop/# Kamagra oral jelly USA availability
sildenafil tablet online india: buy sildenafil – viagra order online australia
Thanks for sharing. I read many of your blog posts, cool, your blog is very good.
Tadalify [url=http://tadalify.com/#]generic cialis online pharmacy[/url] tadalafil vs sildenafil
KamaMeds: KamaMeds – Sildenafil oral jelly fast absorption effect
Sildenafil oral jelly fast absorption effect: Kamagra oral jelly USA availability – Sildenafil oral jelly fast absorption effect
Safe access to generic ED medication: Kamagra reviews from US customers – KamaMeds
Tadalify: Tadalify – generic tadalafil prices
cialis experience reddit: Tadalify – Tadalify
Affordable sildenafil citrate tablets for men [url=https://kamameds.shop/#]Non-prescription ED tablets discreetly shipped[/url] Sildenafil oral jelly fast absorption effect
https://tadalify.shop/# Tadalify
Affordable sildenafil citrate tablets for men: Kamagra reviews from US customers – KamaMeds
Kamagra oral jelly USA availability: Fast-acting ED solution with discreet packaging – Safe access to generic ED medication
SildenaPeak: SildenaPeak – SildenaPeak
SildenaPeak [url=http://sildenapeak.com/#]generic viagra buy online india[/url] SildenaPeak
Tadalify: Tadalify – Tadalify
Tadalify: cialis none prescription – Tadalify
SildenaPeak: SildenaPeak – cheap canadian viagra pharmacy
http://sildenapeak.com/# SildenaPeak
overnight cialis: Tadalify – cialis 20 mg best price
Tadalify [url=https://tadalify.com/#]canadian online pharmacy cialis[/url] cialis logo
Fast-acting ED solution with discreet packaging: Sildenafil oral jelly fast absorption effect – Kamagra reviews from US customers
Affordable sildenafil citrate tablets for men: Affordable sildenafil citrate tablets for men – Men’s sexual health solutions online
SildenaPeak: places to buy viagra – viagra from canada no prescription
SildenaPeak [url=https://sildenapeak.shop/#]viagra prescription online[/url] SildenaPeak
Sildenafil oral jelly fast absorption effect: ED treatment without doctor visits – Sildenafil oral jelly fast absorption effect
https://sildenapeak.shop/# generic viagra 150 mg pills
side effects of cialis daily: Tadalify – does cialis make you harder
Tadalify: Tadalify – Tadalify
SildenaPeak [url=https://sildenapeak.shop/#]SildenaPeak[/url] cost of generic viagra
Tadalify: Tadalify – Tadalify
sildenafil 100mg tablets uk: SildenaPeak – buy viagra cheap online uk
Tadalify: Tadalify – Tadalify
Affordable sildenafil citrate tablets for men: Affordable sildenafil citrate tablets for men – Sildenafil oral jelly fast absorption effect
https://kamameds.shop/# ED treatment without doctor visits
Affordable sildenafil citrate tablets for men: Safe access to generic ED medication – Kamagra oral jelly USA availability
Affordable sildenafil citrate tablets for men [url=http://kamameds.com/#]Compare Kamagra with branded alternatives[/url] Affordable sildenafil citrate tablets for men
SildenaPeak: SildenaPeak – generic viagra online best price
SildenaPeak: viagra 100mg online in india – where to buy generic viagra in canada
cialis free trial offer: Tadalify – cialis manufacturer coupon lilly
buy viagra online in south africa: SildenaPeak – canada viagra
Tadalify [url=http://tadalify.com/#]when should i take cialis[/url] Tadalify
Compare Kamagra with branded alternatives: Non-prescription ED tablets discreetly shipped – Non-prescription ED tablets discreetly shipped
https://tadalify.com/# Tadalify
SildenaPeak: can i buy viagra without prescription – SildenaPeak
Tadalify: Tadalify – tadalafil liquid fda approval date
Affordable sildenafil citrate tablets for men [url=https://kamameds.shop/#]Sildenafil oral jelly fast absorption effect[/url] Fast-acting ED solution with discreet packaging
Kamagra oral jelly USA availability: Compare Kamagra with branded alternatives – Affordable sildenafil citrate tablets for men
SildenaPeak: SildenaPeak – SildenaPeak
SildenaPeak: SildenaPeak – generic viagra discount
SildenaPeak [url=https://sildenapeak.shop/#]SildenaPeak[/url] buy viagra uk pharmacy
best price for cialis: Tadalify – cialis generic best price
http://tadalify.com/# Tadalify
SildenaPeak: women viagra online no prescription – order viagra from india
SildenaPeak: sildenafil 10 mg daily – viagra online paypal canada
cialis for ed: what does generic cialis look like – tadalafil no prescription forum
Non-prescription ED tablets discreetly shipped [url=https://kamameds.com/#]Non-prescription ED tablets discreetly shipped[/url] Non-prescription ED tablets discreetly shipped
ED treatment without doctor visits: KamaMeds – Kamagra oral jelly USA availability
SildenaPeak: SildenaPeak – SildenaPeak
Tadalify: Tadalify – Tadalify
https://kamameds.shop/# ED treatment without doctor visits
viagra uk order: buy viagra online free shipping – SildenaPeak
KamaMeds [url=https://kamameds.com/#]KamaMeds[/url] ED treatment without doctor visits
how can i get a prescription for viagra: SildenaPeak – SildenaPeak
amoxicillin 500mg price: can i buy amoxicillin online – order amoxicillin online
SteroidCare Pharmacy: prednisone cost 10mg – buy prednisone no prescription
IverGrove: ivermectin and blood thinners – ivermectin capsule
prednisone 2.5 mg daily [url=http://steroidcarepharmacy.com/#]generic prednisone 10mg[/url] SteroidCare Pharmacy
CardioMeds Express: CardioMeds Express – lasix generic name